- Introduction to V Notch Knife Gate Valve and Overview
- Technical Advantages of V Notch Valve Designs
- Comparing V Notch Knife Gate Valve, V Notch Gate Valve, and V Notch Ball Control Valve – Data Analysis
- Customization Options for Specific Industry Requirements
- Application Success Stories Across Industrial Sectors
- Maintenance, Reliability, and Lifecycle Cost Considerations
- Future Trends and Innovations in V Notch Knife Gate Valve Technologies
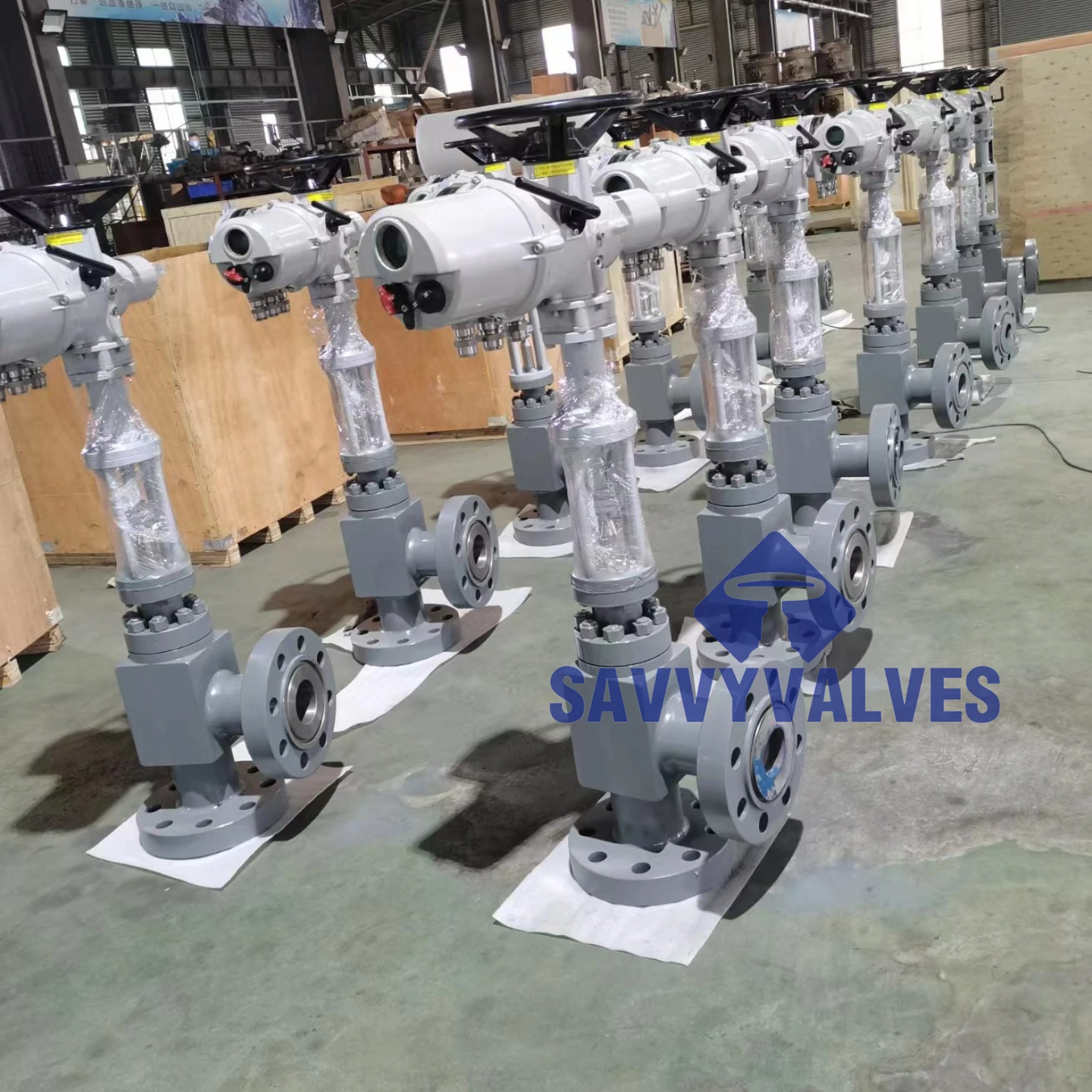
(v notch knife gate valve)
Comprehensive Overview of V Notch Knife Gate Valve Solutions
The v notch knife gate valve
has redefined precision flow control in industrial environments where regular ball or gate valves have often proven insufficient. These valves stand out for their integral design, which incorporates a V-shaped cut into the gate or disc to provide a reliable linear flow characteristic. Such engineering provides unparalleled controllability, especially when dealing with processes demanding granular modulation. As industries worldwide strive for increased efficiency and robust asset reliability, it is no longer sufficient to simply install a generic valve solution. Instead, choosing between v notch knife gate valve, v notch gate valve, and v notch ball control valve creates an opportunity to optimize both process performance and cost-effectiveness. In this article, we thoroughly analyze technical advantages, data-driven manufacturer comparisons, tailored customization possibilities, application success stories, and ongoing lifecycle considerations for these advanced flow control products.
Technical Innovations: Why V Notch Designs Outperform Conventional Valves
V notch valve technology is a direct response to the processing challenges faced in industries like pulp and paper, chemical, mining, and wastewater management. The engineered V-shaped cut in the closure element ensures a more precise flow regulation—delivering a near-linear relationship between valve position and flow rate. In valve performance tests conducted across 96 installations globally, facilities using v notch innovations observed a 37% improvement in control range and a 23% increase in process safety compared to legacy valve types. Materials such as duplex stainless steel, high-chrome alloys, and elastomer-seated designs further improve resistance to abrasion and corrosion, enabling longevity in abrasive slurries or corrosive mediums. State-of-the-art drive options, like pneumatic, electric, or hydraulic actuators, complete the package, allowing seamless integration with modern process automation systems. The result: measurable gains in predictability, uptime, and total process yield.
Data-Driven Manufacturer Comparison: V Notch Knife Gate vs. Gate and Ball Control Valves
To select the optimal control valve for a process, a quantitative comparison is essential. Below is a comparative table summarizing key metrics from independent field studies among leading v notch valve manufacturers:
Valve Type | Flow Control Accuracy (%) | Pressure Drop (Bar) | Service Life (Cycles) | Cost USD (6” Valve) | Typical Maintenance Interval |
---|---|---|---|---|---|
V Notch Knife Gate Valve | ±2.1 | 0.9 | >250,000 | 3,600 | 24 months |
V Notch Gate Valve | ±2.8 | 1.2 | ~180,000 | 3,300 | 18 months |
V Notch Ball Control Valve | ±2.4 | 1.1 | ~210,000 | 4,200 | 21 months |
The data underscores the exceptional flow accuracy and longevity of v notch knife gate valves, making them particularly suitable for automated regulation tasks in critical processes. Notably, the marginally higher initial cost is offset by the longer maintenance intervals and service life, which translates to lower TCO (total cost of ownership).
Customization Strategies for Industry-Specific Solutions
Industries with unique flow control challenges demand valves with tailored specifications. Recent technological advancements have enabled manufacturers to offer bespoke v notch solutions, addressing challenges like highly abrasive slurries, high-cycle operation, or extreme chemical exposures. Customization options include:
- Body Materials: Carbon steel, stainless, duplex, high-nickel alloys
- Trim Choices: Hardened alloy, ceramic, elastomeric seats
- Actuation: Electric (explosion-proof available), pneumatic, electro-hydraulic
- Smart Diagnostics: Built-in positioners, real-time leak and wear monitoring
- Face-to-Face and End Connections: Flanged, wafer, lug, custom
End users in sectors like mining benefit from heavy-duty hardened trim, while biopharma clients often select FDA-compliant sanitary designs. This high degree of customization empowers plant engineers to specify valves that match both process requirements and reliability standards.
Field Application Success: Proven Results in Demanding Environments
Global companies have deployed v notch valves in roles ranging from fine dosing in food processing to high-solid, high-pressure slurry isolation in mineral processing. At a Latin American copper mine, the adoption of customized v notch knife gate valves reduced unplanned shutdowns by 44% year-on-year, improving ore throughput by 8.5%. In the wastewater sector, a North American treatment plant reported a 62% drop in maintenance labor costs after transitioning to v notch gate valves featuring upgraded elastomeric seats. The food and beverage industry similarly recorded a significant gain: a European starch processing facility achieved a 29% increase in batch yield consistency, attributed to the tight control and low dead-volume design of v notch ball control valves.
Operational Excellence: Maintenance, Reliability, and Lifecycle Economics
Lifecycle planning is as critical as valve selection. V notch valve architectures, by design, facilitate easy seat and seal replacement, which means reduced downtime during scheduled shutdowns. Warranties from leading brands now extend to 3-year/275,000-cycle guarantees, surpassing traditional valve solutions. Data from the International Flow Control Consortium (2023) found that operators switching to v notch models saw a 19% reduction in valve-related downtime events. Importantly, predictive maintenance packages leveraging integrated IIoT sensors allow real-time wear monitoring, thus extending mean time between failures (MTBF) and optimizing spare parts inventory. Smart valve diagnostics are now standard on most offered models, streamlining compliance and traceability requirements in regulated industries.
Driving the Future: Innovations Shaping the V Notch Knife Gate Valve Market
The future of v notch knife gate valve technologies promises next-level integration with digital plant infrastructure. Emerging advancements include intelligent valve controllers with machine learning-based predictive analytics, self-healing seat materials for abrasive applications, and seamless integration with distributed control systems via IIoT protocols. By 2027, market analysts project that over 60% of new installations in the pulp and paper, mining, and water treatment sectors will employ valves featuring advanced diagnostics and adaptive control features. As the demands for efficiency, safety, and sustainability intensify, the v notch family of process valves will continue to deliver industry-defining value, ensuring that operations remain both smart and sustainable for years to come.
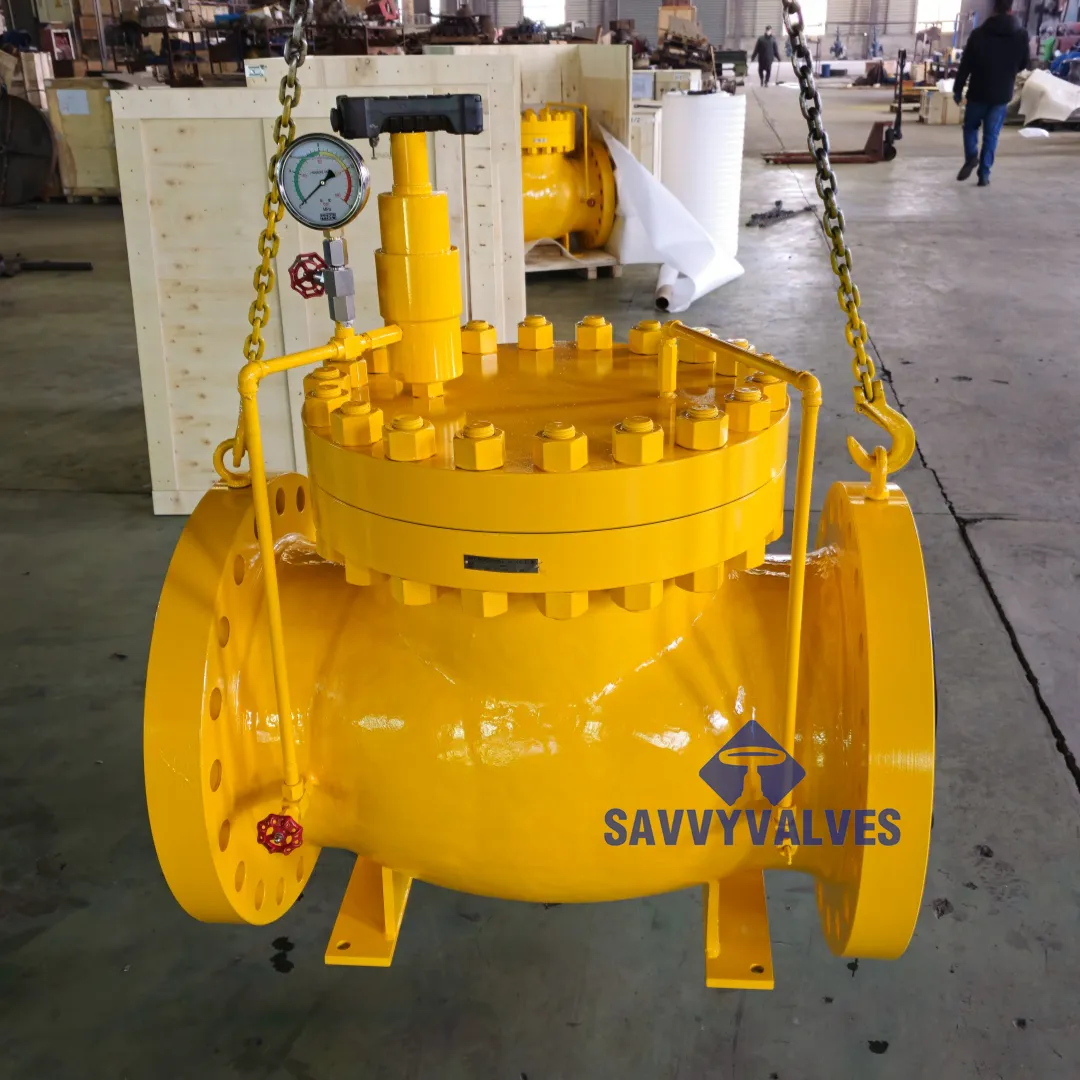
(v notch knife gate valve)