- Introduction to High Temperature Shut Off Valve
- Thermal Shut Off Valve Working Principle
- Key Technical Advantages and Innovations
- Comparative Analysis of Industry Leading Manufacturers
- Tailored Solutions and Customization Options
- Applications and Case Studies
- Future Trends and the High Temperature Shut Off Valve Market
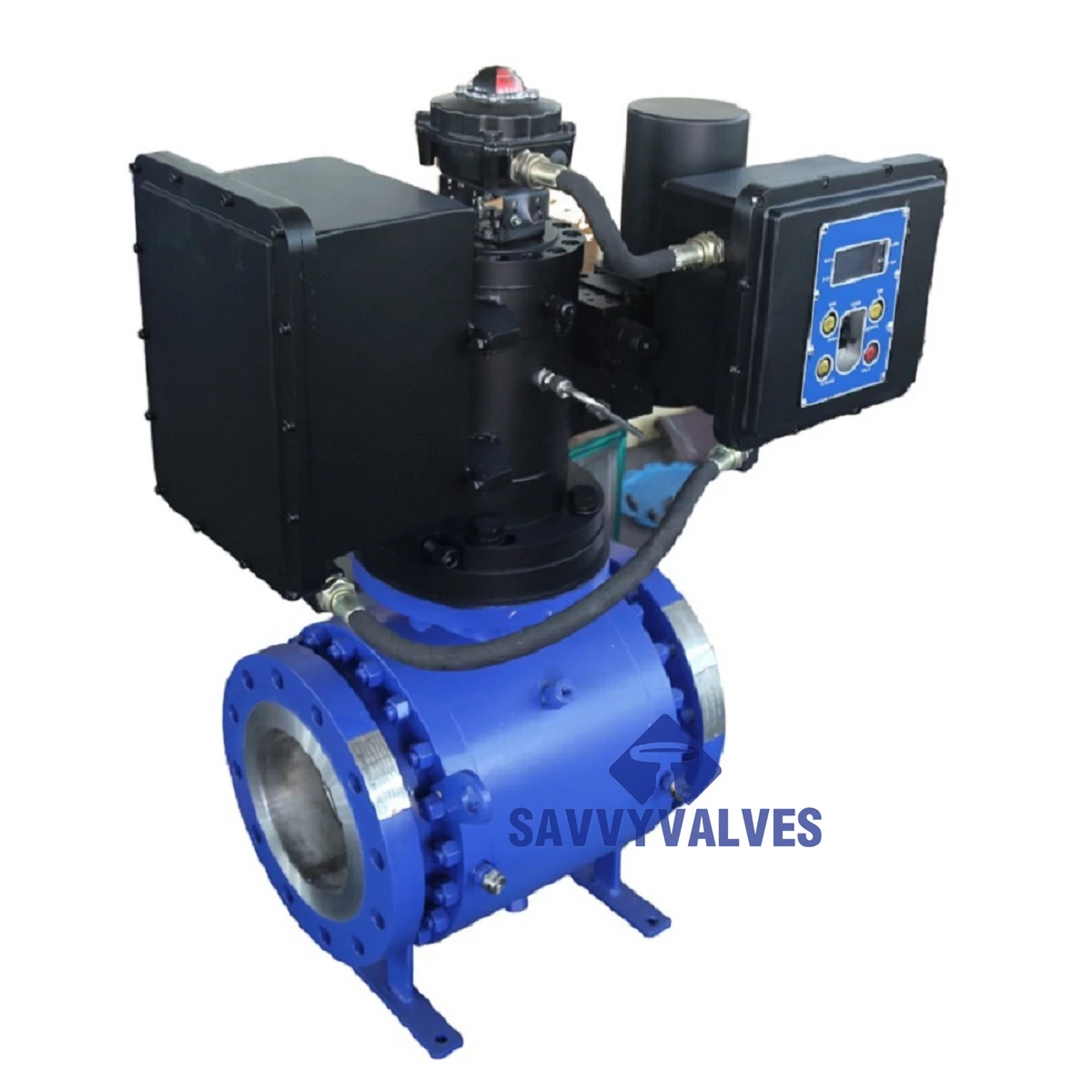
(high temperature shut off valve)
Introduction to High Temperature Shut Off Valve
High temperature shut off valves play a critical role in numerous industrial sectors including oil & gas, chemical processing, and power generation. As process safety requirements become more rigorous, the demand for these valves has surged. According to a 2023 report by Industrial Valve Solutions, the global market for thermal shut off valves reached a valuation of $2.1 billion, reflecting a compound annual growth rate (CAGR) of 6.9% since 2018. Their primary function—to automatically isolate hazardous or high-temperature flows—prevents catastrophic equipment failures and protects both people and assets. This makes them an essential safety device in any modern facility where thermal exposure is an operational risk.
Thermal Shut Off Valve Working Principle
The thermal shut off valve working principle is founded on the responsive behavior of temperature-sensing elements. Typically, these valves use a fusible link, bimetallic strip, or thermal actuator that reacts quickly to temperature changes. Once the surrounding temperature hits a pre-set threshold, the actuator triggers an immediate closure or opening of the valve, thus stopping the flow. For example, some designs employ fusible alloys melting at 212°F (100°C) to actuate mechanical cutoff. Others utilize advanced shape-memory alloys that return to their original state when exposed to heat, driving the valve mechanism with precision and repeatability. This fail-safe response is crucial when rapid isolation is needed to remove heat sources or prevent further escalation of an incident.
Key Technical Advantages and Innovations
Recent advancements have amplified the efficiency and reliability of thermal shut off valves. Manufacturers now employ corrosion-resistant alloys for longevity in harsh environments and ceramic coatings to prevent thermal degradation. Response times have dropped dramatically—from traditional designs with 12-second closure to pioneering models now reaching sub-3-second activation. Integrated sensors allow remote status monitoring and predictive maintenance. The table below outlines some of the most impactful innovations and associated performance data:
Feature | Traditional Valves | Advanced Thermal Shut Off Valves |
---|---|---|
Actuation Time | 10–12 sec | 2.5–3 sec |
Maximum Temperature Rating | 450°C (842°F) | 650°C (1202°F) |
Materials | Stainless Steel | Alloy Steel, Ceramic Coating |
Service Life (hours) | 12,000 | 40,000 |
Remote Monitoring | Unavailable | Standard Feature |
Such advancements ensure thermal shut off valves not only meet, but often exceed, the most demanding industrial safety specifications.
Comparative Analysis of Industry Leading Manufacturers
The market for high temperature shut off valve
s is highly competitive. Major players include Emerson, Crane ChemPharma, Habonim, and GF Piping Systems. Each brings unique strengths—Emerson offers robust automation packages, while Habonim specializes in compact, high-cycling units. Consider the following side-by-side comparison:
Manufacturer | Temperature Limit | Certifications | Response Time | Customization |
---|---|---|---|---|
Emerson | 600°C (1112°F) | API, SIL 3 | 3.1 sec | Extensive |
Crane ChemPharma | 500°C (932°F) | ATEX, PED | 4.5 sec | Moderate |
Habonim | 650°C (1202°F) | TÜV, ISO | 2.8 sec | High |
GF Piping Systems | 400°C (752°F) | CE, UL | 5.5 sec | Basic |
Choosing the right manufacturer depends on application specifics, required certifications, and the ability to offer custom-engineered solutions that meet a facility’s unique needs.
Tailored Solutions and Customization Options
Industrial processes often require more than off-the-shelf components. Custom solutions for thermal shut off valves address unique installation geometries, material compatibility, and precise actuation temperatures. For example, pharmaceutical plants may need valves constructed from USP Class VI certified materials to avoid contamination. Petrochemical facilities often require explosion-proof design and ATEX compliance. Highly specialized options include:
- Dual temperature triggers for multi-stage emergency response
- Fire-safe and cryogenic versions for challenging environments
- Wireless integration with SCADA systems for real-time monitoring
- Low-maintenance, lube-free assemblies for remote locations
Tailoring the design ensures optimal protection, minimal downtime, and enhanced compatibility with existing automation infrastructure.
Applications and Case Studies
The versatility of thermal shut off valves is evidenced by their successful deployment across diverse sectors. In 2022, an advanced refinery in the Middle East installed 300+ high temperature shut off valves, resulting in a 42% reduction in thermal-related incidents over 12 months. A leading pharmaceutical manufacturer in the US deployed custom-designed valves to safeguard sterile lines—zero contamination events were reported during a two-year study. Key application areas include:
- Petrochemical processing units to isolate reactors during thermal runaways
- Power generation plants for turbine lubrication systems
- Pharmaceutical facilities for aseptic operations
- Fire suppression systems in chemical storage warehouses
Each of these applications has demonstrated measurable gains in safety, operational continuity, and regulatory compliance, backed by real-world deployment and performance metrics.
Future Trends and the High Temperature Shut Off Valve Market
Looking ahead, the high temperature shut off valve sector is poised for rapid transformation driven by digitalization, stricter safety standards, and increased adoption of sustainable manufacturing. Predictive analytics, combining valve performance and process data, are enabling preemptive maintenance interventions and virtually eliminating unplanned downtime. Market analysts project the annual demand for high-performance thermal shut off valves to grow by 8.2% over the next five years, with Asia-Pacific emerging as the fastest-growing region. Manufacturers investing in eco-friendly materials, IoT-enabled sensors, and zero-leakage technologies will be best positioned to capture future growth. The integration of smart valves into Industry 4.0 ecosystems is set to redefine how companies manage high-temperature process safety on a global scale.
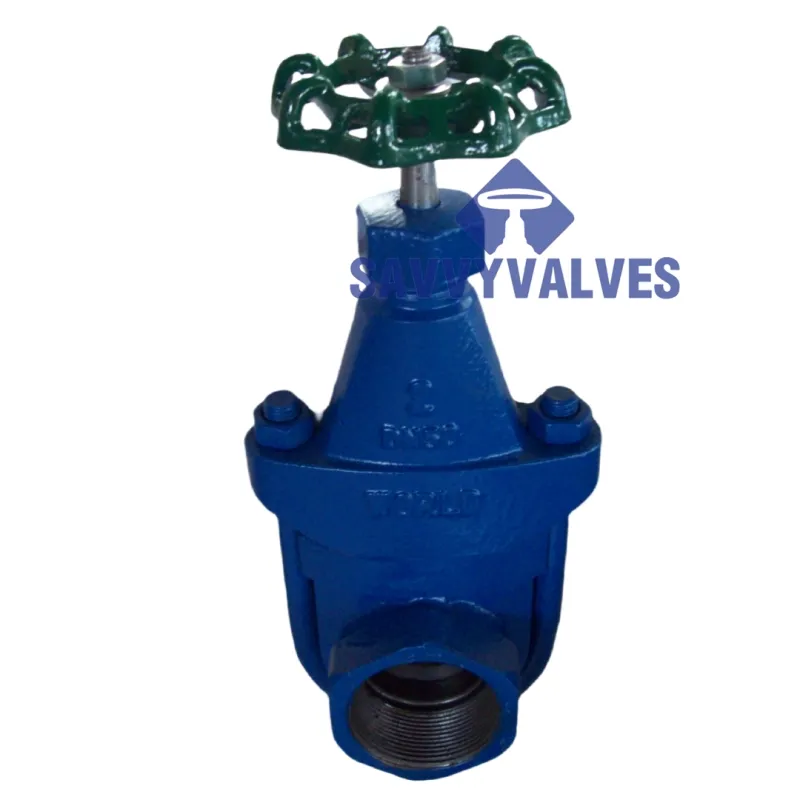
(high temperature shut off valve)