- Introduction to control valves
and their significance - Understanding different types of control valves in instrumentation
- Exploring types of control valves in hydraulic systems
- Comparative data: Technical advantages and manufacturer overview
- Tailoring control valve solutions to precise application needs
- Real-world application case studies and practical insights
- Conclusion: Control valves as drivers of industrial efficiency
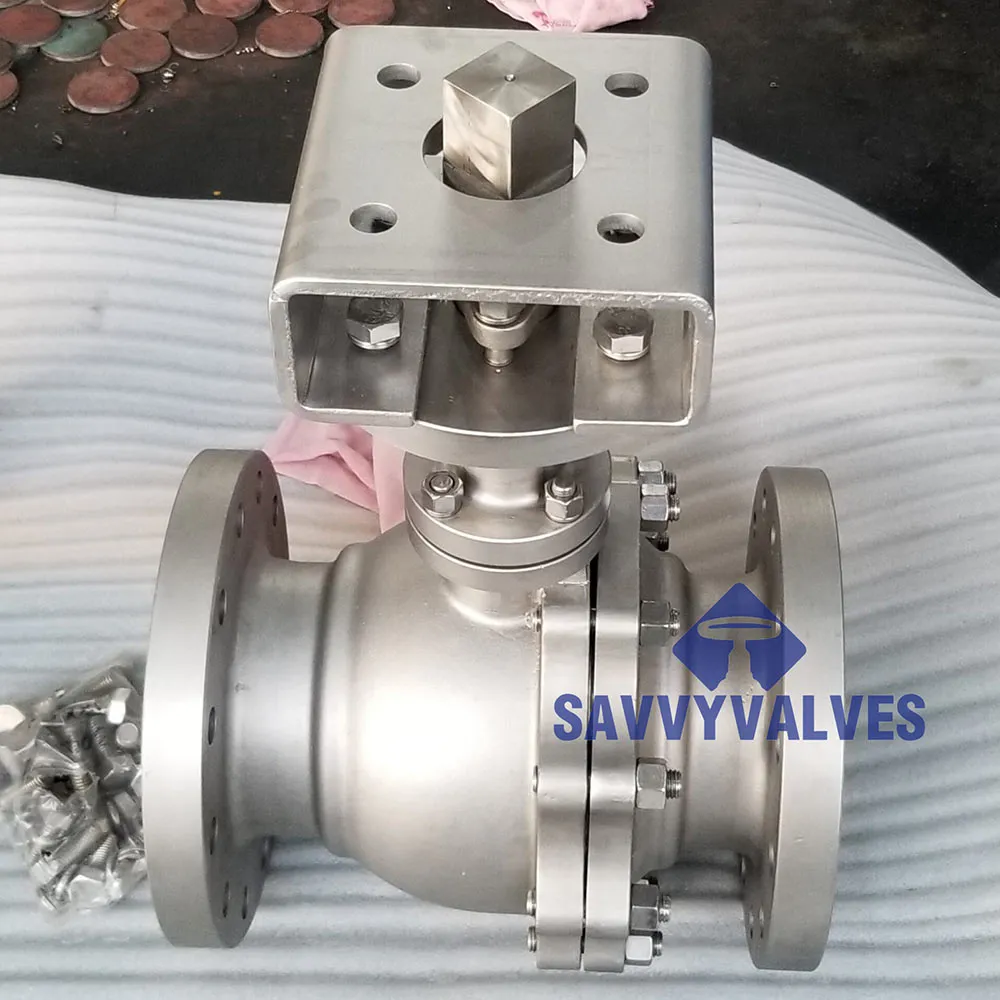
(control valves)
Introduction: Control Valves and Their Critical Role in Modern Industries
Control valves are integral to the automated regulation of fluids in various industries. As the backbone of process control systems, these engineered devices are responsible for modulating the flow, pressure, temperature, and liquid levels in pipelines and vessels. Approximately 60% of process disturbances in manufacturing can be traced to valve or actuator issues, highlighting the critical dependence of industries on reliable control valves. Due to their ability to enhance process safety, minimize wastage, and improve product quality, the demand for advanced control valves grows consistently. The global control valves market size exceeded $7.1 billion USD in 2023 with a projected CAGR of 6.2% through 2030, reflecting the widespread recognition of their technical and operational significance.
Diving Deep: Types of Control Valves in Instrumentation
The instrumentation sector leverages an array of control valves tailored for precision operations and accurate process modulation. The most common types of control valves in instrumentation include:
- Globe Valves: Favored for linear motion and accurate throttling, globe valves offer tight shutoff and minimal leakage, making them ideal for flow regulation.
- Ball Valves: Characterized by their quarter-turn action, ball valves excel in on-off applications and feature high durability even under strenuous conditions.
- Butterfly Valves: Compact and cost-effective, butterfly valves are suited for applications where space is a constraint and moderate sealing is adequate.
- Diaphragm Valves: Utilized for corrosive or viscous fluids, diaphragm valves prevent contamination and ensure precise control in aseptic environments.
Hydraulic Applications: Types of Control Valves in Hydraulic Systems
Hydraulic systems rely heavily on various control valves to manage high-pressure fluid dynamics. The main types of control valves in hydraulic system design include:
- Pressure Control Valves: Essential for maintaining optimal pressure within hydraulic circuits. Examples are relief, sequence, pressure reducing, and unloading valves.
- Flow Control Valves: These valves regulate the speed of actuators by modulating fluid flow. Common forms are needle, throttle, and proportional flow valves.
- Directional Control Valves: These define the path of fluid by permitting, stopping, or diverting flow. Spool, poppet, and rotary types are prominent, each chosen based on response time and leakage tolerances.
Technical Advantages & Manufacturers: Comparative Analysis
Selecting the right control valve requires a comparative view of technical specifications and manufacturers’ reputations. The following table summarizes commonly used types and their technical strengths, as well as a snapshot of manufacturer offerings:
Valve Type | Primary Application | Max Pressure (psi) | Leakage Rate | Cycle Life | Leading Manufacturers |
---|---|---|---|---|---|
Globe Valve | Precise flow regulation | 4500 | <0.0001 cc/min | 500,000+ | Emerson, Flowserve |
Ball Valve | On/Off, full bore | 6000 | <0.001 cc/min | 1,000,000+ | Kitz, Cameron |
Butterfly Valve | Space-constrained applications | 232 | Moderate | 250,000+ | AVK, Crane |
Diaphragm Valve | Corrosive & aseptic | 290 | <0.0002 cc/min | 400,000+ | GEMÜ, Saunders |
Hydraulic Pressure Control Valve | Hydraulic pressure control | 5000 | <0.001 cc/min | 750,000+ | Parker, Bosch Rexroth |
Technical advantage is often application-dependent. For instance, ball valves surpass others in on-off cycling life, whereas globe valves are favored for fine control. Manufacturers such as Emerson and Bosch Rexroth invest heavily in R&D, bringing to market innovations like wireless diagnostics and ultra-low leakage technologies. When evaluating suppliers, consider not just product quality, but also after-sales support, digital integration, and lifecycle cost.
Customizing Control Valve Solutions for Specialized Needs
No two process systems are identical; thus, custom control valve configuration is a critical service offered by leading manufacturers. Customization options range from material selection—such as stainless steel, Hastelloy, or PTFE linings—to actuation types, including pneumatic, electric, or electro-hydraulic operators. Advanced modelling tools now enable process engineers to simulate valve performance under exacting site conditions before procurement.
For complex operations, hybrid valve assemblies combine multiple functions—such as fail-safe mechanisms with position feedback—ensuring redundancies and regulatory compliance. When designing bespoke solutions:
- Specify media, temperature, pressure, and flow rate to select optimal seat and trim materials.
- Incorporate smart positioners for remote diagnostics, especially in harsh or inaccessible locations.
- Implement modular valve body designs to facilitate rapid maintenance and minimize downtime.
Practical Insights: Case Studies of Control Valve Deployments
To illustrate best practices and outcomes, consider these real-world examples:
- Petrochemical Refinery: Faced with excessive flow variability and process disturbances, the facility adopted smart globe valves with integrated sensors. The adjustment reduced unscheduled process interruptions by 23% and improved control accuracy by 18%.
- Pharmaceutical Manufacturing: Diaphragm valves were custom-built using PTFE linings for aggressive sterile solutions. Automated SIP (Sterilize-in-Place) features led to a measurable 29% reduction in cleaning cycle times.
- Steel Mill Hydraulic Actuation: Engineers replaced aging hydraulic pressure control valves with digital feedback models. Result: a 17% reduction in energy consumption and near-elimination of pressure spikes, protecting sensitive down-line equipment.
- Municipal Water Plant: Adoption of triple-offset butterfly valves in space-limited pump stations resulted in a 32% decrease in valve footprint and a 14% boost in annual flow consistency.
Conclusion: Harnessing Control Valves for Peak Process Performance
In conclusion, control valves serve as the guardians of operational consistency and industrial safety across countless processes. By understanding the critical distinctions between types of control valves in instrumentation, those designed for hydraulic systems, and the array of technical features provided by top manufacturers, businesses can realize tangible process improvements. Whether selecting standardized or custom-engineered valves, integrating advanced diagnostics, or deploying data-driven maintenance, the strategic use of pressure and flow control technologies underpins sustainable competitiveness. As industries pursue higher efficiency, safety, and output quality, the centrality of high-performance control valves is only set to expand.
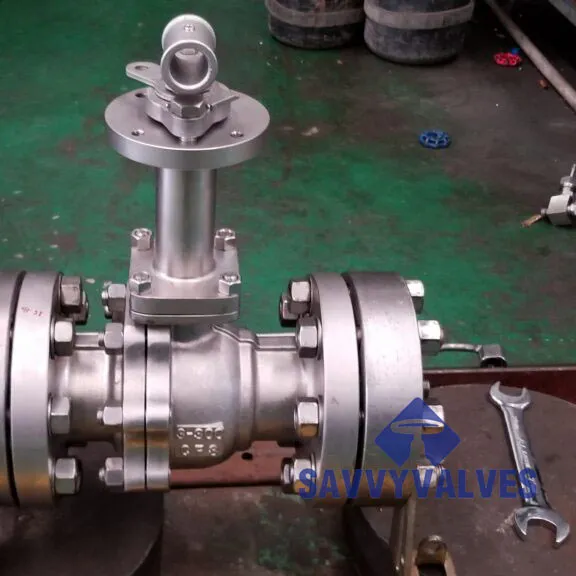
(control valves)