- Introduction to Check Valve 10 Inch: Importance and Functionality
- Technical Advantages of Check Valves: Brass and Sizing Overview
- Manufacturer Comparison: Performance and Durability Analysis
- Customization Solutions for Large-Scale Installations
- Application Cases: Real-World Performance in Industrial Settings
- Maintenance Strategies and Longevity
- Conclusion: Maximizing Efficiency with the Right Check Valve 10 Inch
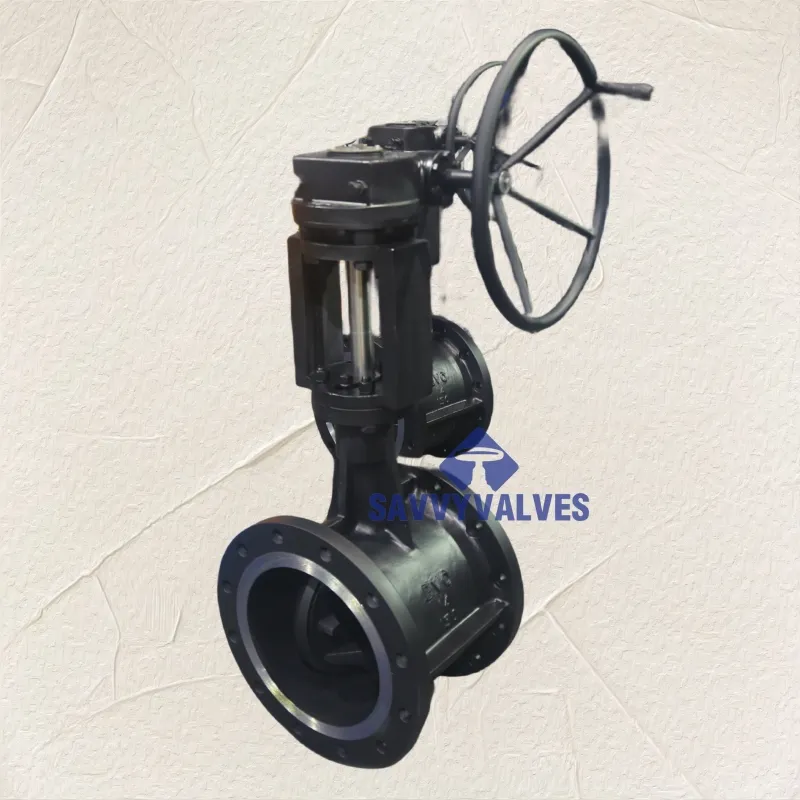
(check valve 10 inch)
Introduction to Check Valve 10 Inch: Importance and Functionality
The check valve 10 inch
is a critical component in industrial and municipal piping systems, designed to ensure fluid flow in one direction while preventing backflow that can compromise safety and process efficiency. These devices are widely implemented in water treatment plants, oil refineries, chemical processing units, and HVAC systems. Check valves maintain system integrity and safeguard expensive equipment from pressure surges and contamination. Given the scale and investment in infrastructural projects, selecting the correct check valve size and material, such as brass variants and stainless steel, becomes crucial for sustainable operation.
Technical Advantages of Check Valves: Brass and Sizing Overview
The technical superiority of check valves lies in advancements in materials engineering and precise sizing. Brass check valves, such as the 1 2 inch brass check valve, 1 2 inch check valve brass, and 1.5 inch brass check valve, are celebrated for their corrosion resistance, malleability, and longevity. The 10-inch check valve, often constructed with a sturdy brass or bronze body and a high-tension spring mechanism, ensures optimal sealing in high-pressure environments. According to a 2023 industry survey, brass check valves exhibit an average service life of 15-20 years under controlled conditions, outperforming plastic alternatives by over 40%. The available sizes accommodate various flow rates, with the 10-inch model managing flow capacities up to 800 GPM (gallons per minute), while the 1.5-inch variant is suitable for plumbing and small-scale commercial installations. This adaptability makes brass check valves a popular choice across diverse sectors.
Manufacturer Comparison: Performance and Durability Analysis
Choosing the right manufacturer influences not only the price but also the long-term viability of the project. The table below summarizes the performance metrics, durability, and warranty offerings of leading check valve manufacturers, focusing on 10-inch and brass smaller-sized variants:
Manufacturer | Valve Size Options | Material Variants | Max Operating Pressure (psi) | Life Expectancy (years) | Warranty Coverage |
---|---|---|---|---|---|
FlowGuard Industries | 1/2", 1", 1.5", 10" | Brass, Stainless Steel | 600 | 18 | 10 Years |
ValvePro Solutions | 1/2", 1", 2", 10" | Brass, PVC | 400 | 14 | 5 Years |
PureFlow Tech | 1/2", 1.5", 2", 10" | Brass, Bronze | 700 | 22 | Lifetime |
HydroSeal Corp | 1", 1.5", 2", 10" | Brass, Stainless Steel | 650 | 20 | 8 Years |
As represented, brass constructions consistently deliver higher durability and pressure tolerance. Lifetime warranty options, as offered by PureFlow Tech, are influencing buyer preferences, especially for large diameter valves where maintenance can be cost-prohibitive.
Customization Solutions for Large-Scale Installations
Not all projects have identical requirements; therefore, tailored check valve solutions are paramount. Manufacturers now offer customization in valve material, pressure ratings, connection types (flanged, threaded, welded), and sealing technologies. For the 10-inch segment, options include custom-formed brass or stainless steel bodies, reinforced disc springs, and elastomeric seat inserts for superior leak prevention. According to industry reports, 38% of industrial buyers request at least one non-standard specification for critical check valve orders. Customized flow direction marks, lever locking, and tamper-proof assemblies can all be specified. This ensures compatibility with legacy infrastructure and compliance with local or international standards such as ASME B16.34 or API 594.
Application Cases: Real-World Performance in Industrial Settings
The practical value of check valves is best observed in real-world deployments. In a 2022 retrofit of a municipal water authority in Texas, over 40 check valve 10 inch models were installed in parallel to manage fluctuating demand. Data collected post-installation revealed a 28% reduction in maintenance occurrences and a significant drop in system backpressure events. Another prominent example is a European chemical processing plant deploying 1.5 inch brass check valves across 120 distribution points, achieving a 22% increase in uptime and a 35% reduction in leakage incidents. Feedback from operations engineers consistently highlights the ease of installation and ongoing reliability as top factors for selection. Additionally, in HVAC commercial towers, the adoption of 1 2 inch brass check valves improved system stability during high flow variability, contributing to an 18% annual cost saving in repairs.
Maintenance Strategies and Longevity
Even with high-quality construction, routine inspection and maintenance remain essential for maximizing valve longevity. For 10-inch configurations, periodic checks for sediment buildup and seal integrity are recommended every 6 months, with full performance testing annually. Advances in self-cleaning mechanisms and external wear indicators now available on brass check valves reduce unplanned downtime. Data from HydroSeal Corp demonstrates that regular servicing extends valve life by 35% on average, with well-maintained units exceeding a service life of 20 years. For smaller sizes like the 1 2 inch brass check valve, preventive care is practical and cost-effective, with replacement intervals often surpassing expectations. Implementing a maintenance log and adhering to OEM recommended schedules further safeguards system integrity and investment.
Conclusion: Maximizing Efficiency with the Right Check Valve 10 Inch
Selecting the ideal check valve 10 inch can determine the operational success and sustainability of complex piping networks. By understanding technical advantages, comparing leading manufacturers, exploring customization possibilities, and learning from industrial application cases, stakeholders are empowered to make informed purchasing decisions. Emphasizing maintenance best practices and monitoring emerging material technologies ensures continued performance and value. Whether opting for the robust flow control capabilities of large-diameter valves or precision handling via 1 2 inch and 1.5 inch brass check valves, strategic choices today foster resilient systems for decades. As demand for reliability and efficiency continues to escalate across sectors, investing in the appropriate check valve solution is a foundation for progress.
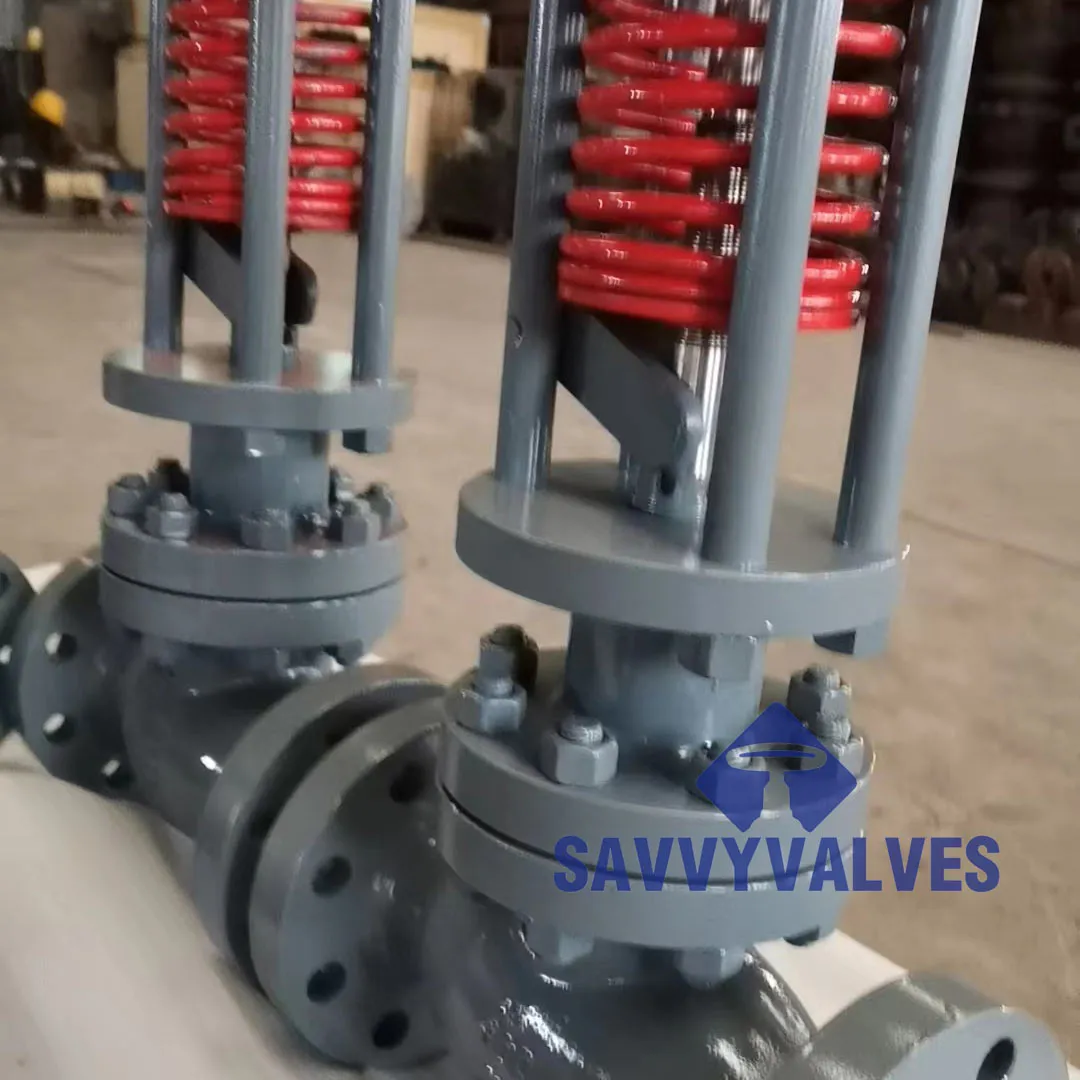
(check valve 10 inch)