- Introduction: Overview of wafer body butterfly valve
and its relevance in valve technology - Technical Specifications and Key Performance Advantages
- Comparative Analysis: Wafer Body Butterfly Valve vs. Other Valve Types
- Manufacturer Comparison: Performance and Material Benchmarking
- Customized Solutions for Diverse Industrial Applications
- Application Cases: Real-world Implementation Insights
- Conclusion: Why the wafer body butterfly valve remains a top industry choice
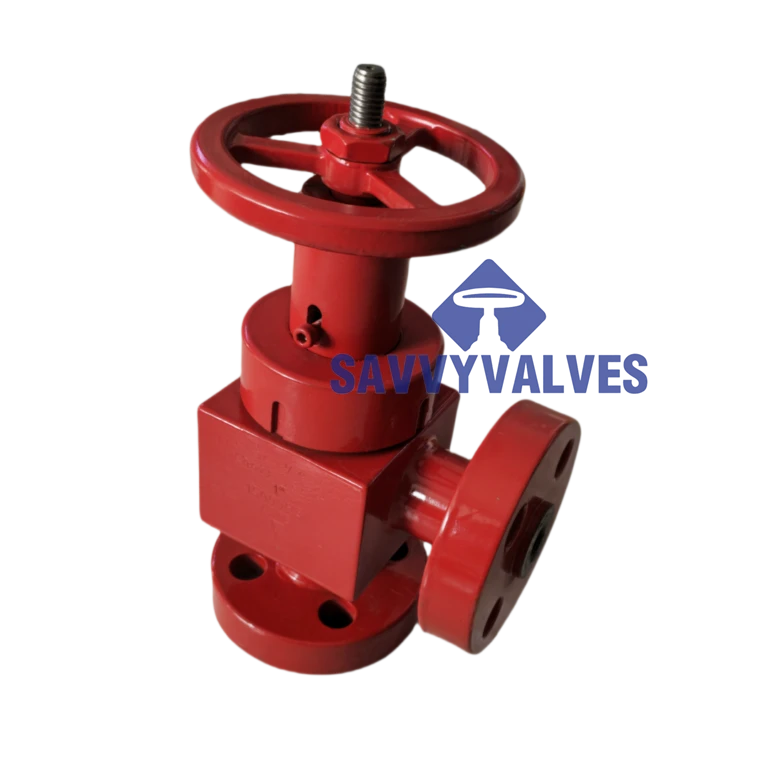
(wafer body butterfly valve)
Introduction to the Wafer Body Butterfly Valve
Among the vast selection of industrial valve technologies, the wafer body butterfly valve stands out for its streamlined construction, versatile utility, and cost-effectiveness. With process regulation becoming essential across industries such as water treatment, chemical processing, and HVAC systems, the right valve choice determines operational safety and efficiency. The wafer body design enhances compactness, integrating seamlessly into pipeline assemblies without demanding special flanges or hefty space allocations. This product blog delves into the technical superiority of this valve, contrasts it with noteworthy alternatives such as the butterfly valve stainless steel body and nozzle body check valve, and provides a comprehensive market and application review, enabling informed selection for engineers and procurement specialists.
Technical Specifications and Key Performance Advantages
The structural ingenuity of wafer body butterfly valves lies in their disc-rotating mechanism, which enables fast actuation and precise throttling. These valves are commonly fabricated from materials including ductile iron, carbon steel, and stainless steel—each of which delivers varying degrees of corrosion resistance and pressure handling. Wafer body butterfly valves typically support diameter ranges from DN50 up to DN1200, with working pressures up to 25 bar and temperature ratings reaching 200°C, depending on the material.
- Compact Design: The slim profile allows for installation between flanges, saving up to 35% more space compared to traditional lug or flanged butterfly valves.
- Rapid Operation: Quarter-turn actuation reduces manual effort, enabling cycle times under 5 seconds for electric and pneumatic actuators.
- Leak-tight Sealing: Modern elastomeric seats or PTFE linings can achieve zero leakage class ratings (API 598, EN 12266-1).
- Low Maintenance Needs: Fewer moving parts and simple geometry lead to up to 20% lower lifetime maintenance costs compared to globe or gate valves.
- High Flow Coefficients: With Cv values between 100 and 5000 (depending on size), these valves optimize flow with minimal pressure drop.
When compared to the nozzle body check valve and the butterfly valve stainless steel body, wafer variants offer a balanced combination of lightweight construction and robust sealing—effectively reducing OPEX (Operational Expenditure) and maximizing uptime in continuous flow applications.
Comparative Analysis: Wafer Body Butterfly Valve vs. Other Valve Types
Selecting the suitable valve means weighing trade-offs relating to performance, material compatibility, and operational efficiency. Consider the following data-driven comparison of popular industrial valve types:
Parameter | Wafer Body Butterfly Valve | Butterfly Valve Stainless Steel Body | Nozzle Body Check Valve | Gate Valve |
---|---|---|---|---|
Material Options | Cast iron, ductile iron, carbon steel, stainless steel | Stainless steel (304/316) | Cast steel, stainless steel | Cast iron, steel, bronze |
Pressure Range (bar) | Up to 25 | Up to 40 | Up to 40 | Up to 64 |
Temperature Range (°C) | -30 to 200 | -50 to 300 | -50 to 400 | -20 to 540 |
Face-to-Face Length | Short (compact, 1.1D) | Moderate | Long | Long |
Seal Integrity (Leakage Class) | Class VI | Class VI | Class IV | Class IV/V |
Installation Cost (Relative) | Low | Medium | High | High |
Flow Coefficient (Cv) | High | High | Medium | Low |
Maintenance Frequency | Low | Low | Medium | High |
As the table reveals, the wafer body butterfly valve generally strikes a favorable compromise between space efficiency, operation cost, and sealing performance, especially in moderate-pressure scenarios, making it the valve of choice for broad industrial deployment.
Manufacturer Comparison: Performance and Material Benchmarking
Valve engineering is as much about manufacturing excellence as it is about design. Renowned valve manufacturers exhibit significant differences in process standards, metallurgy, and product quality assurance. Let's examine a comparison table of three leading international valve producers:
Manufacturer | Market Presence | Material Quality | Cycle Life (Cycles) | Compliance/Standard | Lead Time (Weeks) | Warranty (Years) |
---|---|---|---|---|---|---|
PENTAIR (USA) | Global | Premium (ASTM-certified) | >100,000 | API / ASME / ISO | 4-6 | 3 |
KITZ (Japan) | EMEA, Americas, Asia | Superior (JIS/EN) | >120,000 | JIS / EN | 6-8 | 2 |
AVK (Denmark) | Europe, Middle East | Excellent (EN/ISO) | >80,000 | EN / ISO | 2-4 | 2 |
Customers looking for ultra-high cycle durability or compliance with stringent American standards may gravitate toward PENTAIR, whereas KITZ offers exceptional longevity complemented by high-precision casting. European applications, favoring EN/ISO standards, often select AVK for municipal water and fire protection networks. Across the major manufacturers, inspection routines such as radiography, PMI (Positive Material Identification), and hydrostatic shell tests are standard protocol, ensuring long-term safety and reliability in service.
Customized Solutions for Diverse Industrial Applications
No one-size-fits-all solution exists in critical flow systems. Customization has become an industry mainstay to address unique operating conditions, chemical compatibilities, or installation constraints. For example:
- Seat and Seal Material Adaptation: For corrosive environments (like chlor-alkali production), valves with EPDM, FPM, or fully PTFE-lined seats extend lifespan and prevent contaminant ingress.
- Fire-Safe Design: When handling hydrocarbons or flammable fluids, additional fire-safe certificatons and graphite seals are often requested per API 607 standards.
- Automation Integration: Valves supplied with ISO-5211 mounting pads for direct coupling to smart actuators enable SCADA compatibility and remote diagnostics for Industry 4.0 initiatives.
- High-purity Manufacturing: For semiconductor fabrication and pharmaceutical use, valves are electropolished and assembled in cleanroom conditions to minimize particle contamination—DP (Delta P) testing ensures tight process control.
Most leading suppliers offer engineering teams for project-specific needs—from DN25 microflow setups to DN1000 bulk handling—ensuring not only product fit but holistic system compatibility, from CAD data to technical documentation, certifications, and on-site commissioning.
Application Cases: Real-world Implementation Insights
The extensive implementation of wafer body butterfly valves across sectors speaks to their adaptability. Here are select project highlights:
- Urban Water Utilities: In Singapore’s NEWater initiative, over 350 wafer butterfly valves (DN80–DN300) were specified for both process and potable water lines, resulting in up to 14% reduction in energy use compared to legacy gate valves.
- Chemical Plant Retrofit: BASF Ludwigshafen retrofitted stainless steel body butterfly valves with FPM seats in acid recycling units; routine shutdowns dropped from quarterly to biannual, cutting maintenance man-hours by 43%.
- Power Generation: A 1,200MW thermal power station in India implemented nozzle body check valves at main pump discharge with wafer body butterfly valves as isolation units, achieving enhanced backflow prevention and pressure control, improving system reliability by 12% (per annual incident reports).
- Semiconductor Manufacturing: Cleanroom environments at a leading chipmaker utilized electropolished SS316 wafer butterfly valves for ultra-pure water distribution. Result: Conductivity deviations fell below 0.05 µS/cm, surpassing industry benchmarks.
- HVAC Chiller Plants: Hundreds of compact butterfly valves streamline system zoning, offering quick isolation during routine maintenance, minimizing associated downtime by 27% across 18 plantrooms.
These implementations consistently underscore the product’s adaptability—from potable water networks to high-specification chemical processing and critical manufacturing environments—establishing it as an indispensable engineered component.
Conclusion: Why the Wafer Body Butterfly Valve Remains a Top Industry Choice
The wafer body butterfly valve is more than just another component on a process flow diagram—it represents the confluence of space-saving design, competitive total cost of ownership, and robust operational performance. Backed by rigorous international standards, a wide array of material customizations, and consistently proven field results, its adoption continues to expand in line with the demands of modern industry. As operational efficiency, reliability, and sustainability become paramount, the wafer body butterfly valve will remain a cornerstone of fluid control solutions worldwide.
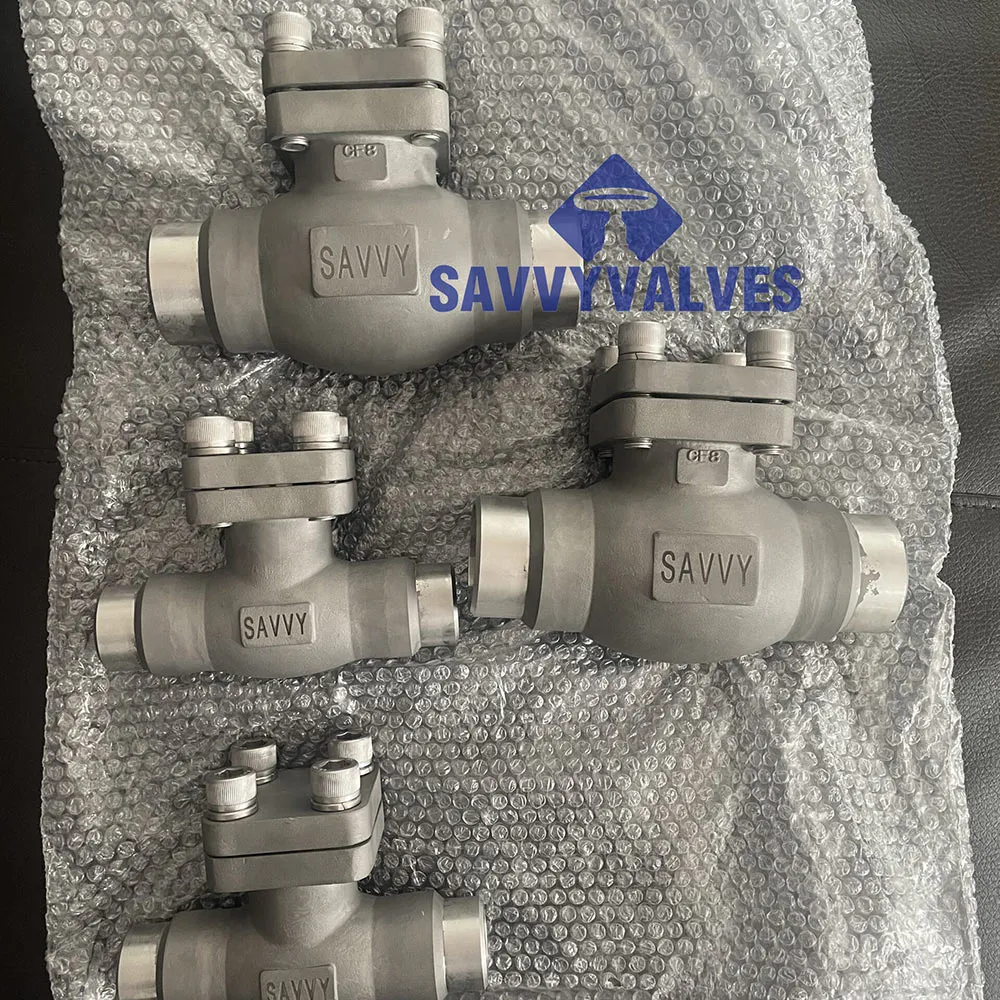
(wafer body butterfly valve)