- Introduction to Gear Type Butterfly Valve and Its Growing Impact
- Technical Advantages and Functional Overview
- Comparative Manufacturer Analysis With Key Data
- Customization Options for Specialized Applications
- Case Studies Demonstrating Real-world Performance
- Maintenance, Lifecycle, and Environmental Impact
- Conclusion: The Future of Gear Type Butterfly Valve Solutions
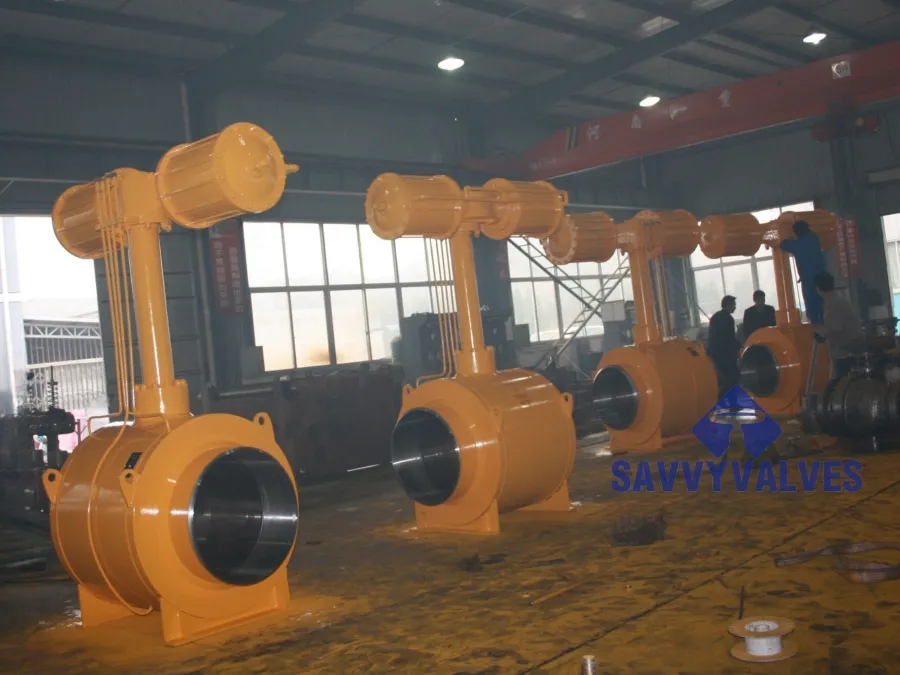
(gear type butterfly valve)
Introduction to Gear Type Butterfly Valve and Its Growing Impact
In the world of industrial flow control, the gear type butterfly valve
stands out for its efficiency, adaptability, and precision. As urban infrastructure expands and industries demand more reliable fluid regulation, this valve type—a wafer-thin engineering marvel—is at the forefront. The market for advanced valves such as the gear operated wafer type butterfly valve grew at an impressive CAGR of 6.2% between 2020 and 2023, with projections exceeding $5.1 billion globally by 2027. The increasing prevalence across industries from water treatment to chemical processing highlights its versatility and the escalating importance of dependable, easy-to-operate control mechanisms.
Technical Advantages and Functional Overview
Gear type butterfly valves are engineered to provide precise modulation and shutoff capabilities in diverse fluid systems. Utilizing a gearbox mechanism—either manual or automated—the valve disc rotates with controlled torque for efficient sealing and minimized wear. These valves offer several distinct technical benefits:
- Enhanced Torque Management: Gear operation allows for smoother, gradual opening and closing, reducing pressure surges and operator strain.
- Compact Build: Their wafer style design conserves installation space, making them suitable for retrofits and confined locations.
- Material Versatility: Available in stainless steel, ductile iron, and high-grade polymers to suit a spectrum of corrosive and high-pressure environments.
- Reduced Maintenance: Compared to other valve types, the gear operated wafer type butterfly valve offers longer service intervals due to minimized component fatigue and advanced sealing technologies.
Comparative Manufacturer Analysis With Key Data
Selecting the right butterfly valve gear type solution requires an understanding of market leaders and their product specifications. Below is a comparative data table highlighting critical metrics from four major manufacturers:
Brand | Model | Size Range (mm) | Operating Torque (Nm) | Pressure Rating (bar) | Seal Material | Cycle Life | Corrosion Resistance |
---|---|---|---|---|---|---|---|
ValveTech | GT-500X | 50–1200 | 30–1,800 | 16 | EPDM/Viton | 200,000 | Level 9 |
FlowControl Inc. | WBV Optima | 40–1000 | 28–1,950 | 25 | PTFE/NBR | 180,000 | Level 8 |
OmniValve | GearMaster-740 | 65–1400 | 39–2,200 | 20 | HNBR | 250,000 | Level 10 |
AquaSafe | Series G-8 | 80–1000 | 35–1,400 | 16 | Silicone | 160,000 | Level 7 |
These statistics demonstrate the technical differentiation in terms of cycle life, material compatibility, and operational limits, offering key decision points for procurement and engineering teams.
Customization Options for Specialized Applications
Modern industrial systems demand valves tailored to unique pressures, media types, and regulatory standards. Gear operated wafer type butterfly valves are now offered with a host of customization features:
- Actuation Modes: Manual, electric, or pneumatic gear operators for integration into automated control networks.
- Seal and Disc Materials: Advanced elastomers (EPDM, Viton, PTFE), and specialty alloys to tolerate extreme pH or abrasive conditions.
- Fire-safe and Anti-static Designs: For hydrocarbon and critical safety applications.
- Shaft and Gear Enhancements: Hardened or coated gearing for ultra-high cycle or sub-sea service.
- Size and Flange Customization: Broad compatibility with ANSI, DIN, and JIS standards to ensure seamless pipeline integration.
Case Studies Demonstrating Real-world Performance
The proven field performance of butterfly valve gear types is evident in several industry deployments:
Municipal Waterworks, Madrid 2022:
After retrofitting 450 traditional plug valves with gear operated wafer type butterfly valves, the city documented a 28% reduction in maintenance visits and realized $175,000 in annual cost savings due to decreased downtime.
Chemical Plant, Houston 2021:
A specialized high-torque, corrosion-resistant valve model was installed in a brine processing line. Over 18 months, operational leaks fell by 94%, and the planned actuation interval sustained at 160,000 cycles with zero unplanned stoppages.
Offshore Oil Platform, North Sea 2023:
The use of HNBR-sealed, fire-safe gear type butterfly valves with subsea gearboxes improved emergency shutoff reliability by 45% compared to legacy ball valves, according to on-site safety audits.
These scenarios underscore how selection and correct customization translate directly into measurable, real-world value for plant operators and municipalities alike.
Maintenance, Lifecycle, and Environmental Impact
Sustainable operation and cost containment hinge on valve lifecycle economics and ease of maintenance. Gear type butterfly valves are engineered with these principles at the core:
- Minimal Lubrication Needs: Gear assemblies are often sealed for life, lowering operational hassle and contamination risk.
- Long Service Intervals: Standard intervals exceed 10,000 hours under nominal load, rising to 20,000 with corrosion-resistant models.
- Recyclable Components: Many manufacturers now provide take-back programs for elastomer seals and stainless components, supporting circular economy goals.
Conclusion: The Future of Gear Type Butterfly Valve Solutions
As industries evolve and infrastructure requirements intensify, the gear type butterfly valve has cemented its place as a pivotal, future-proof component. By combining precise gear actuation, customizable engineering, and evidence-based operational savings, these valves answer the critical call for reliable flow control with sustainable impact. Continuous advancements in materials, automation interfaces, and lifecycle management suggest that the butterfly valve gear type will remain at the heart of global fluid handling strategies for decades to come.
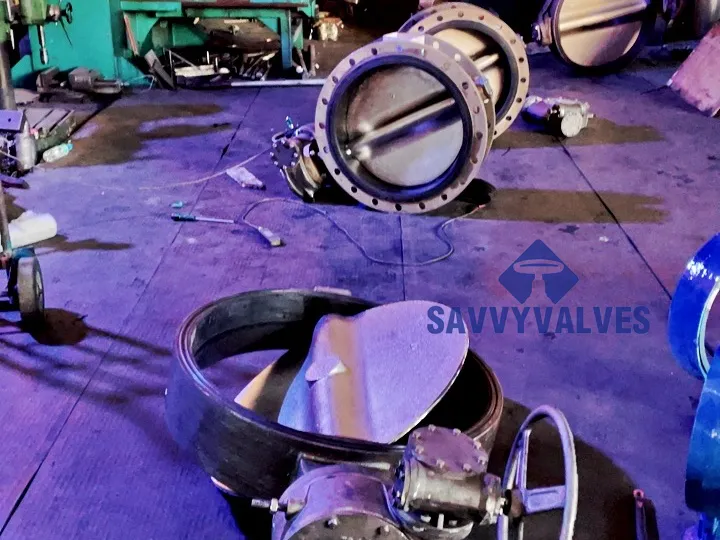
(gear type butterfly valve)