- Introduction to flanged ball valve
and their industrial significance - Technical characteristics and dimensional standards
- Comparative analysis of major manufacturers
- Custom design and engineering options
- Detailed dimensional data and specifications
- Real-world applications and case studies
- Conclusion: The future of flanged ball valve technology
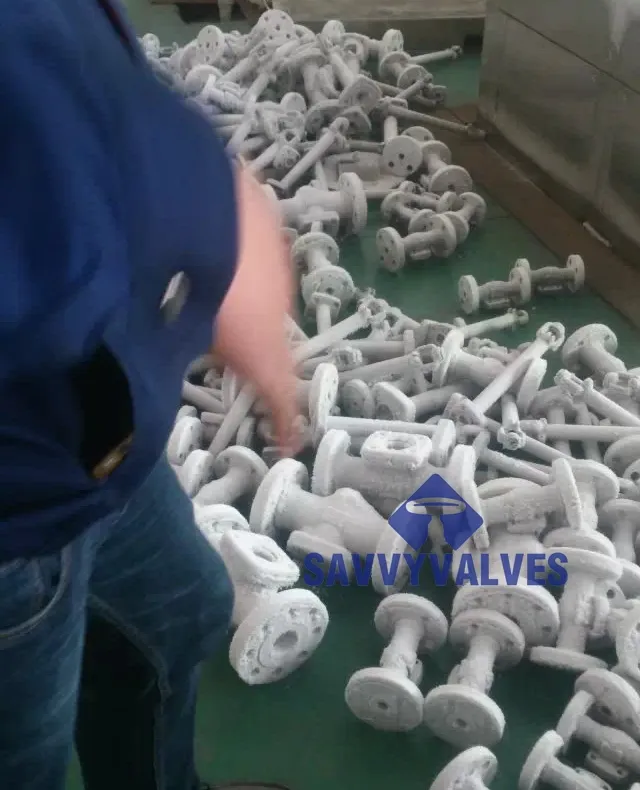
(flanged ball valve)
Flanged Ball Valve: The Foundation of Industrial Fluid Control
In modern fluid infrastructure, the flanged ball valve stands as a cornerstone for ensuring reliable and leak-proof flow management. These valves have been widely adopted across industries such as oil and gas, chemical processing, water treatment, and power generation, due to their straightforward design and impressive performance metrics. The robust flanged connection provides ease of installation, maintenance, and mechanical strength even under high-pressure scenarios. According to a 2023 market report, the global demand for flanged ball valves hit over $6 billion USD, growing at a compound annual growth rate (CAGR) of 5.8%. Their ability to facilitate rapid quarter-turn shutoff and regulate flows with minimal pressure drops makes them invaluable where safety and reliability are paramount.
Technical Characteristics and Standard Dimensions
The defining feature of flanged ball valves is their connection method—integrated flanges that bolt directly onto pipeline systems. This setup ensures secure, repeatable sealing and structural stability. Key technical advantages include:
- Full Bore and Reduced Bore Options: Allowing for tailored flow rates and system capacities.
- Pressure Ratings: Commonly available in Class 150, 300, 600, and higher, supporting both low and high-pressure applications.
- Material Versatility: Bodies constructed from stainless steel, carbon steel, brass, and specialty alloys for compatibility with varying fluids and environmental conditions.
- Automation Compatibility: Can be fitted with pneumatic or electric actuators for advanced process automation.
Manufacturer Comparison: Quality, Cost, and Compliance
Selecting the right supplier involves balancing factors like cost, lead time, technical compliance, and post-sale support. Leading companies—including Emerson (Fisher), Flowserve (Worcester), Crane, and Velan—dominate different industry sectors. Regional manufacturers might offer lower costs but may fall short on documentation and certifications. Below is a comparative table synthesizing key metrics:
Brand | Main Material | Pressure Rating | Size Range (inches) | Certifications | Average Lead Time (weeks) | Warranty (years) |
---|---|---|---|---|---|---|
Emerson (Fisher) | Stainless Steel, Alloy | 150–2500 | 1–24 | API, ISO, CE | 8–12 | 2 |
Flowserve (Worcester) | Carbon Steel, Stainless | 150–600 | 0.5–12 | API, ISO, SIL | 6–10 | 3 |
Crane | Stainless Steel | 150–600 | 1–8 | ISO, CE | 5–8 | 1 |
Velan | Stainless, Alloy | 150–1500 | 1–16 | API, ISO, PED | 8–14 | 2 |
Generic Asian | Carbon, Stainless | 150–300 | 1–12 | ISO, CE | 4–6 | 1 |
Customization and Engineering Flexibility
Not every application can be solved with an off-the-shelf solution. For processes dealing with corrosive media, extreme temperatures, or demanding operational cycles, custom flanged ball valves are engineered with unique seat and seal materials, special coatings, or modified actuator interfaces. Examples include:
- High-Temperature Operations: Utilization of PEEK or metal seats for continuous service above 500°F (260°C).
- Aggressive Chemicals: Cladding wetted parts with Hastelloy, Inconel, or PTFE to withstand acidic or alkaline solutions.
- Fire-Safe Designs: Compliance with API 607 or ISO 10497 fire testing for critical process safety.
- Low-Emission Packing: Fulfilling ISO 15848 or TA-Luft standards to reduce fugitive emissions in environmentally sensitive sectors.
Detailed Dimensional Data: Reference Standards
Dimensioning is central to safe and efficient installation. Engineering teams routinely consult ball valve flanged end dimensions and standardized tables derived from ASME, DIN, or EN norms. These resources provide definitive reference points for every size and pressure class. For instance, the following representative data illustrates typical 4-inch valve dimensions:
Valve Size (inches) | Pressure Class | Face-to-Face Length (mm) | Flange Diameter (mm) | Bolt Circle (mm) | Bolt Holes x Size |
---|---|---|---|---|---|
4 | 150 | 229 | 229 | 190 | 8 x 19 mm |
4 | 300 | 432 | 254 | 210 | 8 x 22 mm |
4 | 600 | 559 | 279 | 235 | 8 x 25 mm |
Industrial Applications and Case Studies
Across sectors, the adoption of flanged ball valves is driven by the pursuit of lifecycle performance, compliance, and operational safety. A notable example from the petrochemical industry illustrates the replacement of 250 legacy gate valves with modern flanged ball configurations in a European refinery. Results after 18 months included:
- Maintenance Reduction: 70% decrease in unscheduled valve service interventions.
- Safety Performance: Zero valve-related leakage incidents reported post-commissioning.
- System Efficiency: Enhanced throughput with 18% lower pressure drop, as quantified during process audits.
The Future of Flanged Ball Valve Technology
The evolution of flanged ball valve solutions is being shaped by advances in digital manufacturing, predictive maintenance, and sustainable material science. Valves are routinely equipped with IoT sensors for real-time health monitoring, while additive manufacturing accelerates the delivery of custom geometries at reduced cost. Industry standards for flanged ball valve dimensions and traceable flanged ball valve dimensions pdf remain foundational, but innovation is propelling the segment into a data-driven era. The combination of robust standards and adaptive manufacturing ensures that flanged ball valves will continue to set benchmarks in safety, efficiency, and compliance for a wide spectrum of global industries.
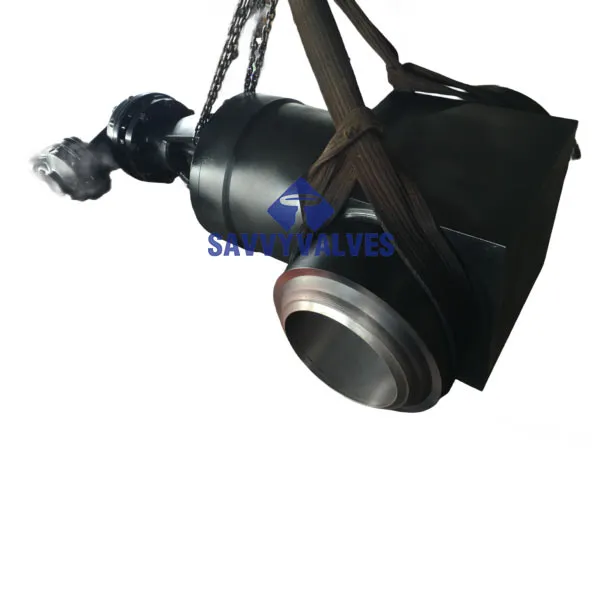
(flanged ball valve)
FAQS on flanged ball valve
Q: What is a flanged ball valve?
A: A flanged ball valve is a type of ball valve featuring flanged end connections for easy installation and removal. These flanges allow secure bolted connections to the piping system. Flanged ball valves are common in various industrial applications due to their strength and sealing capability.
Q: What are ball valve flanged end dimensions?
A: Ball valve flanged end dimensions refer to the standardized sizes and measurements of the valve's flange faces and bolt holes. These dimensions ensure compatibility with piping and meet standards like ANSI, DIN, or JIS. Always check the manufacturer’s datasheet for exact specifications.
Q: Where can I find flanged ball valve dimensions in PDF format?
A: Flanged ball valve dimensions in PDF format can typically be found on valve manufacturers' websites or in industrial product catalogs. Search for "flanged ball valve dimensions PDF" for readily available downloadable documents. These PDFs provide detailed dimension tables and diagrams for various sizes.
Q: How do I select the right flanged ball valve dimensions?
A: Select the right flanged ball valve dimensions based on your piping size, pressure requirements, and applicable flange standards. Refer to official dimension charts or datasheets for accurate sizing. Ensuring proper dimensions helps maintain system compatibility and leak-free operation.
Q: What standards govern flanged ball valve dimensions?
A: Flanged ball valve dimensions are mainly governed by standards such as ANSI, ASME, DIN, and JIS. These standards specify flange size, bolt circle, and thickness for interchangeability. Consult your project’s required standard before purchasing a valve.