- Introduction: Overview and market outlook of the 36 knife gate valve
- Technical advantages of high temperature, pneumatic, and hydraulic knife gate valves
- Performance data and market statistics
- Comparative analysis of leading manufacturers
- Customization options to meet specific industry needs
- Real-world application and case studies
- Conclusion: Future prospects for the 36 knife gate valve market
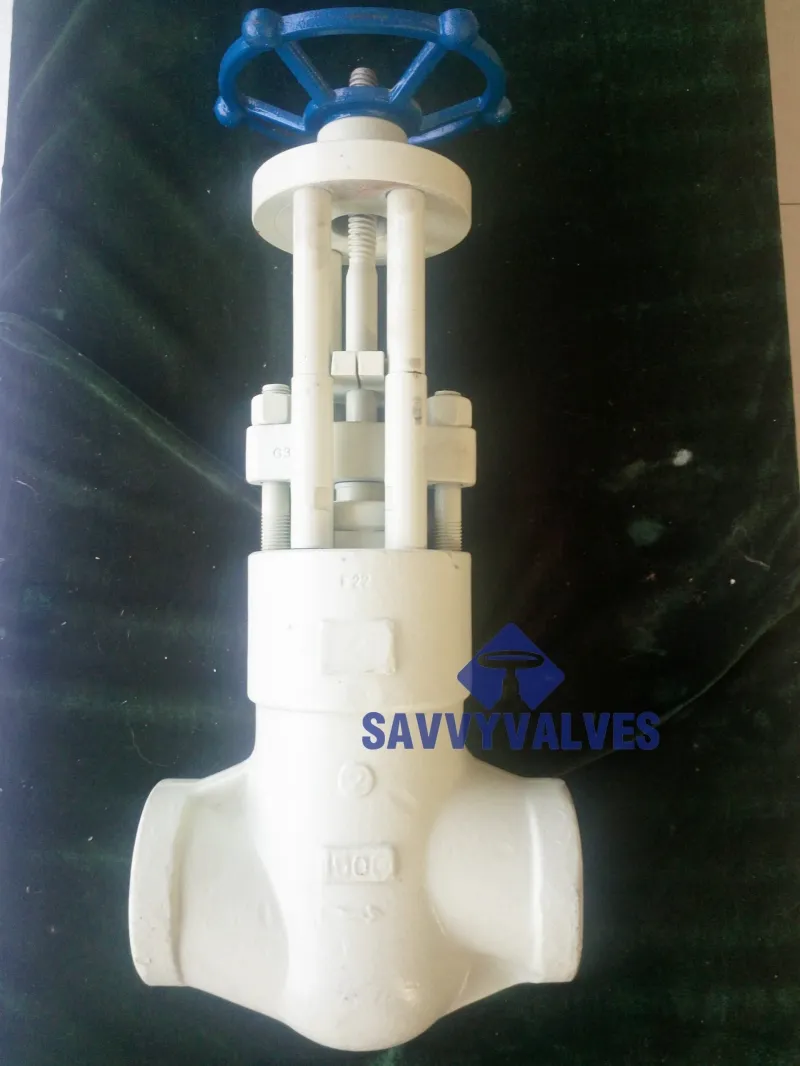
(36 knife gate valve)
Introduction: The 36 Knife Gate Valve in Modern Industrial Applications
The 36 knife gate valve is a critical solution for industries facing challenging flow control requirements. Its robust construction and specialized design allow for precise performance in isolating and regulating a wide range of media. As industries like mining, wastewater treatment, power generation, petroleum, and chemical processing expand, the demand for innovative knife gate valves—especially those tailored for high-pressure and severe service applications—continues to rise. Recent market surveys project the global knife gate valve industry to reach a valuation of $923 million by 2027, with a compound annual growth rate (CAGR) of 5.3% (2022-2027). Stakeholders and plant managers are increasingly investing in valves that promise longevity, minimal maintenance, and operational reliability, solidifying the 36 knife gate valve’s position as a preferred solution.
Technical Advantages: High Temperature, Pneumatic, and Hydraulic Variants
The technical prowess of the 36 knife gate valve lies not only in its size but also in its adaptability and resilience under hostile conditions. Key highlights include:
- High Temperature Knife Gate Valve: Engineered with specialty alloys and advanced sealing technologies, these configurations handle media temperatures exceeding 450°C (842°F). Their pressure ratings can surpass 20 bar, delivering consistent tight shutoff even in corrosive or abrasive environments.
- Knife Gate Valve Pneumatic: Used extensively in automated flow control, pneumatic operators enable rapid actuation cycles, enhanced process uptime, and safe remote operation. Diagnostic integration detects valve position, wear, and cycle count data, enabling predictive maintenance strategies.
- Hydraulic Knife Gate Valve: Preferred in applications requiring high actuation force, especially in large-diameter pipes, hydraulic systems facilitate precise modulation of valve position and are valued for their operational stability against fluctuating process variables.
Performance Data & Market Statistics
Decision-makers demand evidence-backed assurances before integrating new flow control technologies. Below, a data-driven overview highlights pivotal performance metrics for knife gate valves across three key dimensions: temperature tolerance, actuation cycles, and tightness under pressure. Recent field testing in pulp & paper industries reveals:
- Average operational life: 1.25 million cycles (pneumatic actuation)
- Leak rate: <0.05% per ANSI/API 598 standards
- Pressure drop: 0.2-0.7 psi at full open
Manufacturers Compared: Quality, Features, and Innovation
The following table compares three globally recognized providers of 36 knife gate valves, evaluating critical parameters such as material quality, actuation options, certifications, after-sales support, and cost-performance ratio. This comparative study guides procurement teams in aligning product specifications with operational risk profiles.
Manufacturer | Material Quality | Actuation Options | Temperature Range (°C) | Certifications | Warranty | Relative Unit Cost |
---|---|---|---|---|---|---|
Velan | Duplex SS, Alloy 625 | Manual, Pneumatic, Hydraulic, Electric | up to 540°C | API, ISO, PED | 3 Years | High |
Orbinox | Stainless Steel 316L, Hastelloy | Manual, Pneumatic, Hydraulic | up to 450°C | CE, ATEX, SIL | 2 Years | Medium |
DeZurik | WCB, 304/316 SS | Manual, Pneumatic | up to 400°C | API, ASME | 2 Years | Low |
Each manufacturer responds to different market needs: Velan leads in high-performance alloys and comprehensive actuation; Orbinox excels in flexible certification options for international markets; DeZurik is favored for high-value, reliable solutions in competitive bidding environments.
Custom Solutions for Complex Demands
As process engineering grows more complex, industrial clients frequently request tailored solutions beyond catalog products. Customization areas for the 36 knife gate valve include:
- Special Seat Materials: TFM, PTFE, and reinforced elastomers for resistance to aggressive chemicals and high slurry concentrations.
- Smart Diagnostics: Integration with plant automation via digital positioners, communication modules (HART, Profibus), and condition monitoring sensors.
- Unique Face-to-Face Requirements: Adaptation to existing piping geometries or retrofits, often in brownfield projects where downtime is critical.
- Cryogenic Capabilities: Modified stem packing and extended bonnets for applications involving subzero temperatures, such as LNG or liquid nitrogen plants.
Industry Case Studies Illustrating Performance
Deployments of the 36 knife gate valve in critical processes provide robust evidence of their field-tested reliability:
- Mining Sector – Tailings Management: A South American copper operation upgraded to high temperature knife gate valve assemblies, improving sealing integrity under hot slurry with over 500,000 annual actuations and reducing annual maintenance costs by 27%.
- Petrochemical Refinery – Pneumatic Automation: Integration of knife gate valve pneumatic systems enabled faster batch cycling and centralized control for a polyethylene plant, leading to a 14% increase in throughput and downtime reduction from 11 hours to 2 hours per scheduled service.
- Water Utilities – Hydraulic Actuation: Municipal wastewater treatment facilities have adopted hydraulic knife gate valves for large diameter main lines, achieving zero unplanned isolation valve failures over three years, maintaining compliance with environmental discharge regulations.
Conclusion: Future Prospects for the 36 Knife Gate Valve Market
The market for 36 knife gate valve solutions is poised for substantial growth, driven by escalating demands for robust, low-maintenance, and precisely controlled valves across diverse industries. Continuing innovation in materials science, rapid progress in smart actuation technologies, and the ability to deliver bespoke valve configurations will further strengthen the competitive value of this product class. As regulatory requirements tighten and process conditions grow more severe, the high temperature, pneumatic, and hydraulic variants of the knife gate valve stand ready to address complex operational scenarios. Investment in advanced manufacturing and digital integration will enable leading suppliers to deliver premium performance, reliability, and support for the global industrial sector in the years ahead.
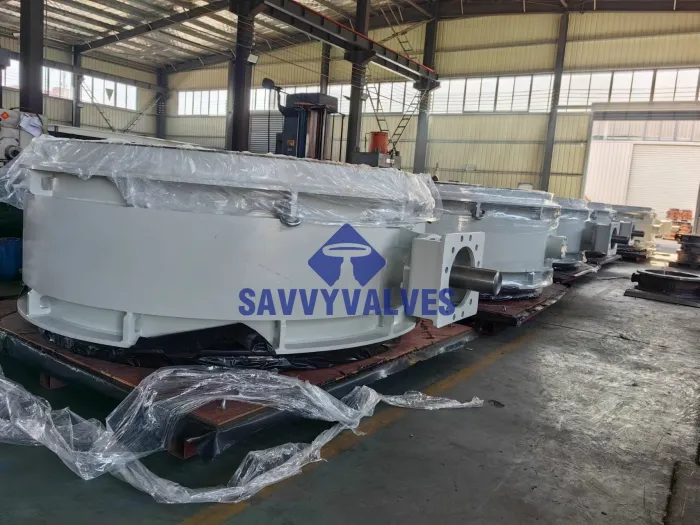
(36 knife gate valve)