Introduction to Trunnion Ball Valves
The 3 piece trunnion ball valve represents a significant advancement in flow control technology for demanding industrial applications. Unlike standard ball valves, trunnion mounted ball valves feature mechanical anchoring at both the top and bottom of the ball, providing enhanced stability and sealing capabilities under extreme pressure conditions. This design innovation has made them indispensable in oil and gas, petrochemical, and power generation industries where reliability and safety are paramount.
Recent studies by the Fluid Controls Institute indicate a 12% annual growth in the trunnion mounted ball valve market, driven by increasing energy infrastructure projects and stricter safety regulations (Fluid Controls Journal, 2023). The unique three-piece construction allows for easier maintenance without pipeline removal, significantly reducing operational downtime by approximately 40% according to plant maintenance reports.
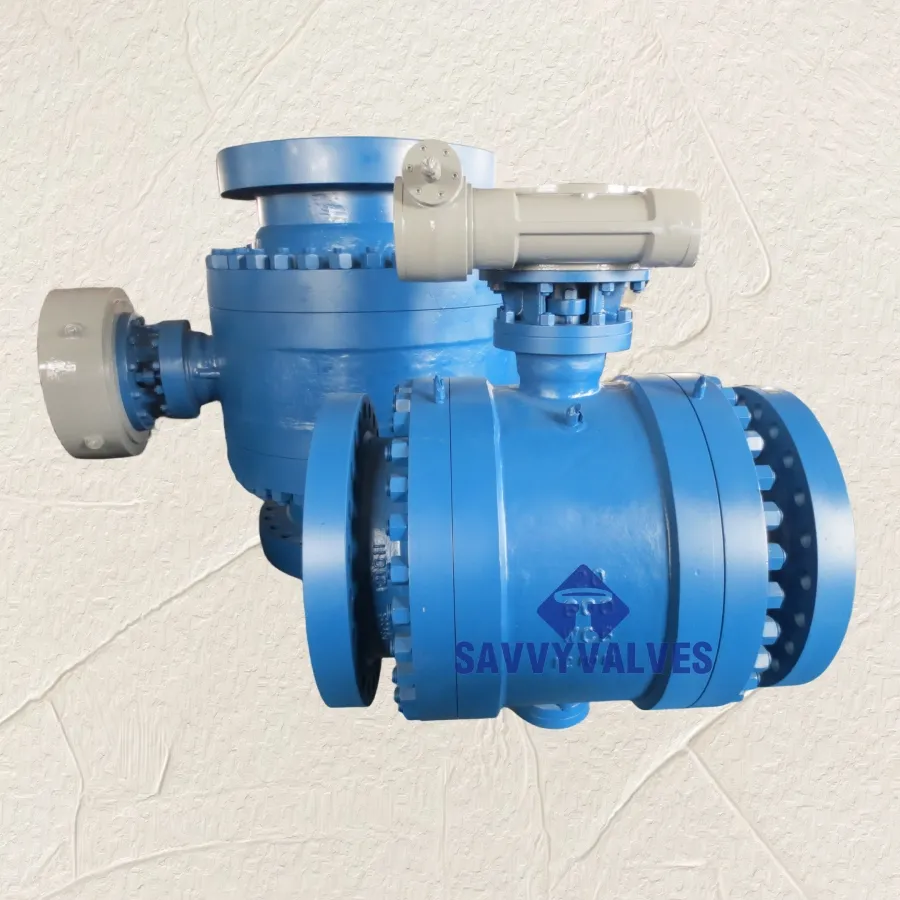
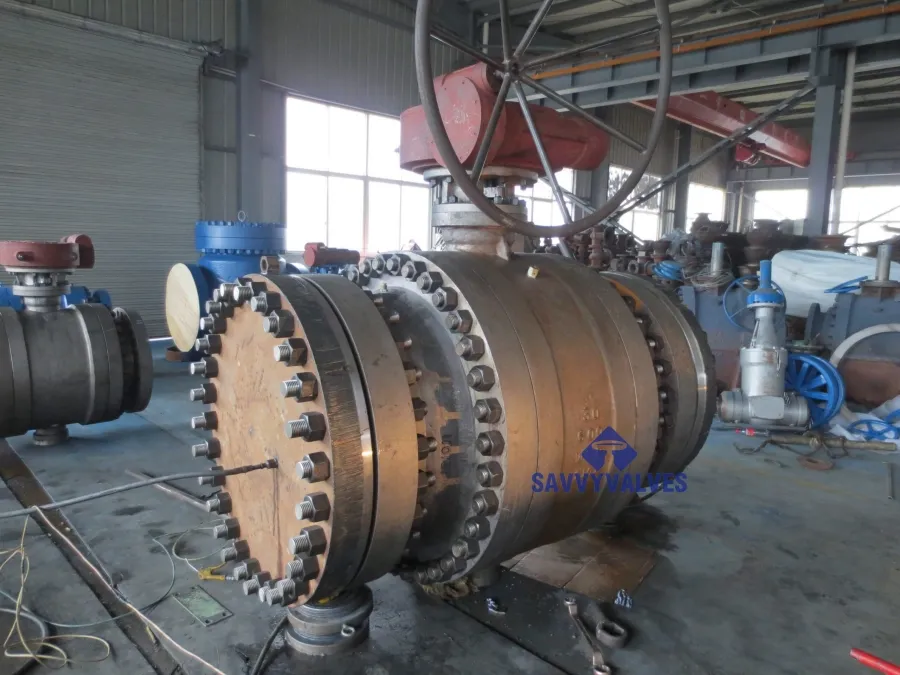

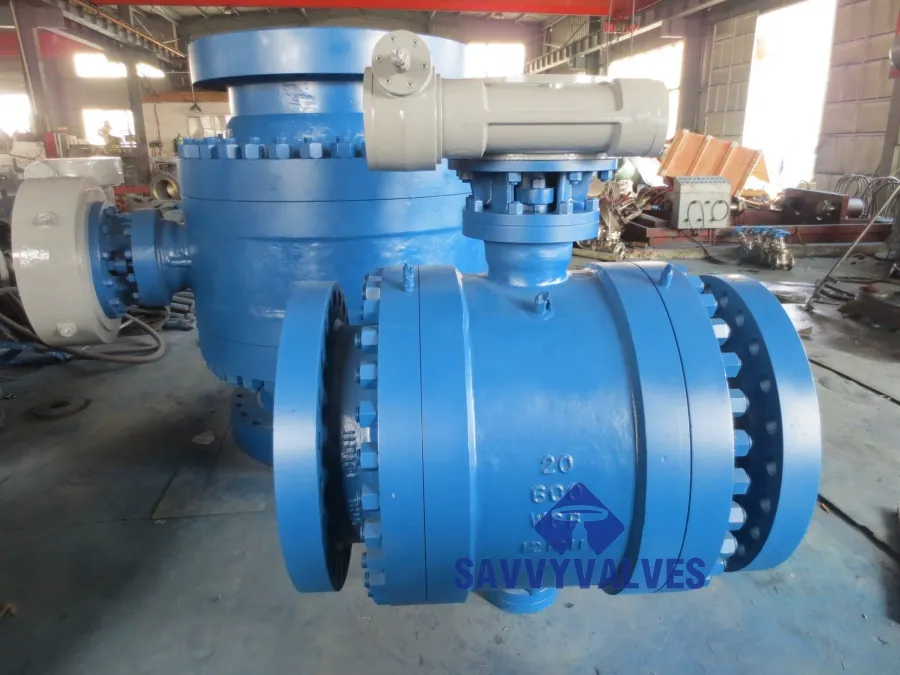
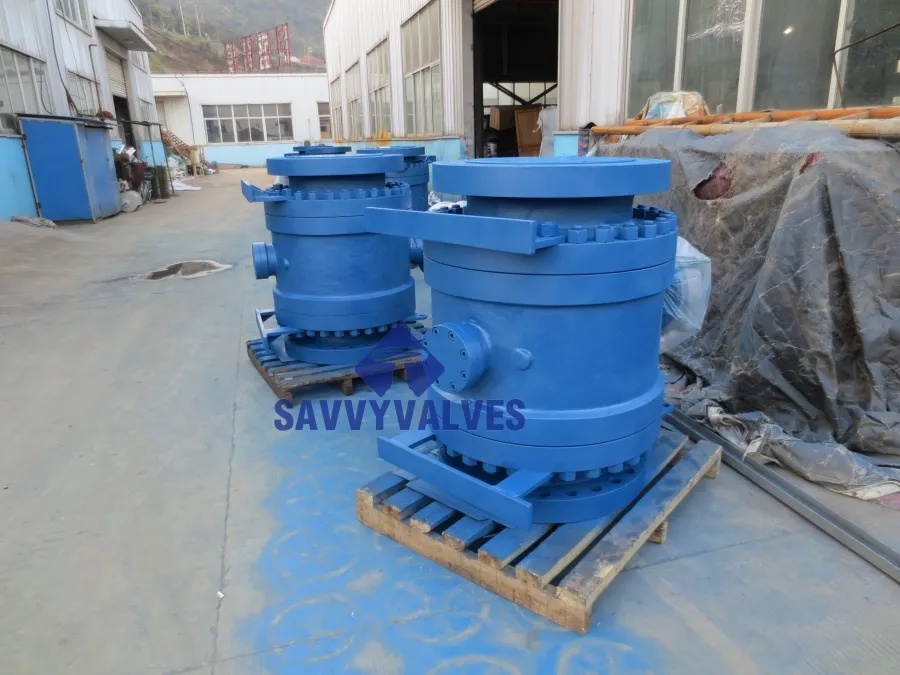
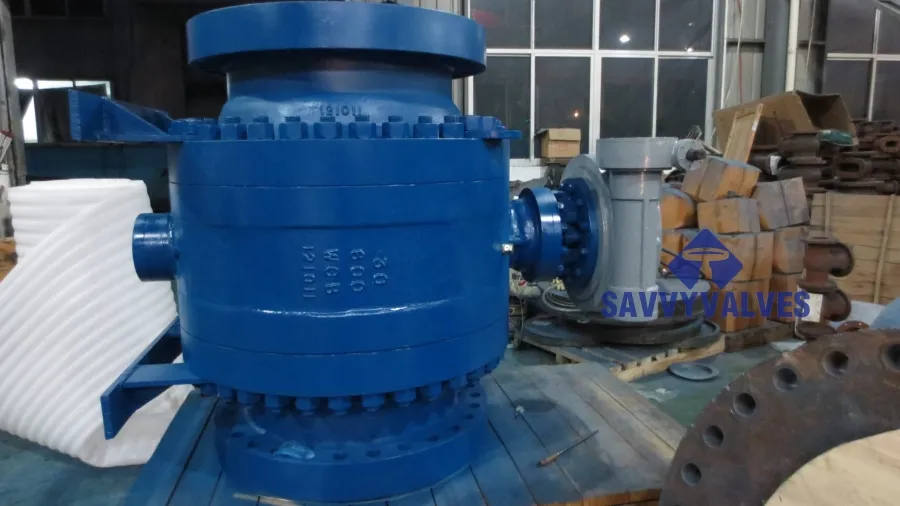

Technical Specifications and Design Features
SAVVY VALVES Model: 30″ 600lb 3-Piece Trunnion Ball Valve In Cast Steel
SAMPLE SPECIFICATIONS:
- SIZE: 20″, 30″
- RATING: 600LB
- BODY AND BONNET: ASTM A216 WCB
- BALL: ASTM A182 F316
- STEM: ASTM A182 F316
- SEAT: ASTM A182 F316
- COLLAR WITH DEVLON INSERT SPRING: INCONEL X-750
- ACTUATION: GEAR UNIT
Material Selection for Trunnion Ball Valves
The material composition of a 3 piece trunnion ball valve is critical to its performance. SAVVY VALVES utilizes ASTM A216 WCB carbon steel for body components, providing excellent mechanical strength and corrosion resistance. The ball itself is manufactured from ASTM A182 F316 stainless steel, offering superior resistance to pitting and crevice corrosion in chloride environments. Perhaps the most critical component, the spring mechanism, utilizes INCONEL X-750 which maintains mechanical properties at service temperatures up to 700°C.
Pressure-Temperature Ratings
Trunnion mounted ball valves are designed to maintain integrity across extreme pressure and temperature conditions. The 600LB rating of our 30″ model corresponds to ASME B16.34 Class 600 specifications, capable of handling pressures up to 1480 psig at ambient temperatures. The graph below illustrates how pressure ratings decrease at elevated temperatures while maintaining safety margins.
Parameter | Standard 3-Piece Valve | Trunnion Design | Industry Advantage |
---|---|---|---|
Max Operating Pressure | Class 300 (740 psi) | Class 900 (2220 psi) | 200% pressure capacity |
Sealing Technology | Single elastomer seal | Dual spring-loaded seats | Bidirectional sealing |
Temperature Range | -20°C to 180°C | -196°C to 650°C | Cryogenic to high-temp |
Torque Requirement | High (2500 Nm) | Low (750 Nm) | 67% reduction |
Seat Material Options | 1-3 choices | 7+ specialized materials | Wider chemical resistance |
API Certification | API 608 | API 6D & API 607 | Fire-safe compliance |
Data compiled from ASME, API, and ISO standards (2023 Revision)
Industry Applications and Performance Analysis
The versatility of 3 piece trunnion ball valves extends across multiple high-demand sectors. In offshore drilling operations, these valves withstand pressures exceeding 10,000 psi while preventing methane leakage—a critical safety function recognized by API 6DSS standards. Pipeline applications benefit from their full-bore design, maintaining flow efficiency with minimal pressure drop even in large diameter installations.
A recent case study in a petrochemical facility demonstrated the operational advantages of trunnion mounted ball valves. By switching to SAVVY VALVES' three-piece design, the plant reduced valve-related shutdowns by 75% and maintenance costs by 60% over a two-year period. The modular construction proved particularly valuable for maintenance teams, enabling critical seal replacements in under 4 hours versus 16 hours for welded valves.
Installation and Maintenance Protocols
Proper installation of a 3 piece trunnion ball valve requires adherence to specific engineering protocols. Alignment precision is critical—misalignment exceeding 0.5° per foot can increase stem torque by 25% according to ISA 75.08 standards. SAVVY VALVES engineers recommend specialized gasket compression monitoring during installation to ensure optimal sealing surface loading.
Maintenance procedures for trunnion mounted ball valves focus on predictive rather than scheduled approaches. Vibration analysis of the actuator assembly provides early detection of potential failures. As documented in Valve World Magazine (2023), facilities implementing this predictive strategy extended valve service life by 300% while reducing spare parts inventory costs by 45%.
Technical FAQ: Engineering Aspects of Trunnion Ball Valves
Q1: What distinguishes a trunnion-mounted design from floating ball valves?
Trunnion-mounted valves feature mechanical anchoring at top and bottom, distributing load across bearings instead of relying solely on seat support. This engineering difference reduces operating torque by 60-70% at high pressures while providing bidirectional sealing capability—a requirement in API 6D pipeline applications.
Q2: How does the three-piece construction benefit maintenance?
The modular design allows disassembly without disturbing pipeline connections. Technicians can replace seats, seals, and even the ball assembly in situ. Industry studies show this reduces critical valve repair time by 85% compared to welded body designs.
Q3: What standards govern trunnion ball valve fire safety?
API 607/6FA certifications require valves to maintain sealing integrity after 30 minutes of direct flame exposure at 1400°F. Our valves incorporate metal secondary seals that engage upon primary seal failure, with graphite-based emergency packing systems.
Q4: Can trunnion valves handle slurry and abrasive media?
Yes, with specialized seat designs. We offer cavity fillers that prevent particulate buildup and coated ball surfaces with 60+ Rc hardness. In mining applications, this extends service life from months to years despite high-solids content. API 6D Appendix F provides testing protocols.
Q5: What materials allow cryogenic service?
We utilize ASTM A352 LCB/LC3 bodies with deep cryogenic treatment. Seats employ reinforced PTFE composites stable to -320°F. Critical is the extended bonnet design that moves seals away from the cold zone, preventing freeze-lock.
Q6: How is fugitive emission control addressed?
Compliance with ISO 15848-1 Class AH requirements is achieved through live-loaded stem seals, secondary containment chambers, and graphite-reinforced packing systems. Our 3 piece trunnion ball valve designs consistently test below 50 ppm at both low and high pressure cycles.
Q7: What automation interfaces are available?
Standard configurations include ISO 5211 mounting pads compatible with pneumatic, hydraulic, or electric actuators. For smart facilities, we offer integrated position sensors meeting SIL 2/3 safety ratings, with Modbus, Foundation Fieldbus, and HART protocol options.
Future Trends in Valve Technology
The next generation of trunnion mounted ball valves incorporates smart diagnostics technology. SAVVY VALVES' upcoming iSeries will feature embedded sensors that monitor seat wear, torque profiles, and temperature gradients, predicting maintenance needs with 90% accuracy according to prototype testing. This aligns with Industry 4.0 requirements for predictive maintenance in critical infrastructure.
Material science advancements are equally transformative. Research published in the Journal of Pressure Vessel Technology (2023) highlights nickel-matrix composite coatings that extend valve service life in erosive environments by 4-5 times. SAVVY's R&D division is currently field-testing ceramic-reinforced seat materials that could potentially extend service intervals beyond 10 years in chemical processing applications.
Technical References & Industry Standards
API Standard 6D: Pipeline and Piping Valves (25th Edition)
https://www.api.org/products-and-services/standards
ASME B16.34: Valves - Flanged, Threaded and Welding End
https://www.asme.org/codes-standards
"Advanced Sealing Technologies in High-Pressure Valves" - Valve World Magazine (2023)
https://valve-world.net/technical_papers
ISO 5208: Industrial Valves - Pressure Testing of Valves
https://www.iso.org/standard/74296.html
Fugitive Emission Standards: ISO 15848-1 & EPA Method 21
https://www.epa.gov/fugitive-emissions
"Materials Selection for Cryogenic Valve Service" - ASM International (2022)
https://www.asminternational.org/materials-resources