Industry-Leading Forged Steel Lift Check Valve Solutions
The forged steel lift check valve represents a critical component in modern fluid control systems, designed to prevent reverse flow in pipelines carrying liquids and gases. With the global industrial valve market projected to reach $116.5 billion by 2027 (GVR Report, 2023), advanced lift check valve technology is becoming increasingly vital. SAVVY VALVES CO.,LTD. stands at the forefront of this evolution, leveraging cutting-edge manufacturing techniques to produce superior API 602-compliant valves that outperform industry standards in reliability, durability, and operational efficiency.
API 602 Pattern Forged Lifting Check Valve
Our flagship product represents the pinnacle of lift check valve engineering: Size:1″ | Rating:150LB | Body & Bonnet: ASTM A105 | Disc: ASTM A105+STELLITE 6 | Spring: INCONEL X-750 | Seat: ASTM A105+STELLITE 6
This precision-engineered valve operates on the fundamental principle of the lift check mechanism - utilizing gravity and flow dynamics to control disk movement. When forward flow occurs, pressure lifts the disk off its seat, allowing fluid passage. As flow decreases or reverses, the disk returns to its seat, creating a positive seal against backflow.
"Forged steel valves provide superior mechanical strength compared to cast alternatives, especially in high-pressure applications where material integrity is non-negotiable." - International Journal of Pressure Vessels and Piping, 2022
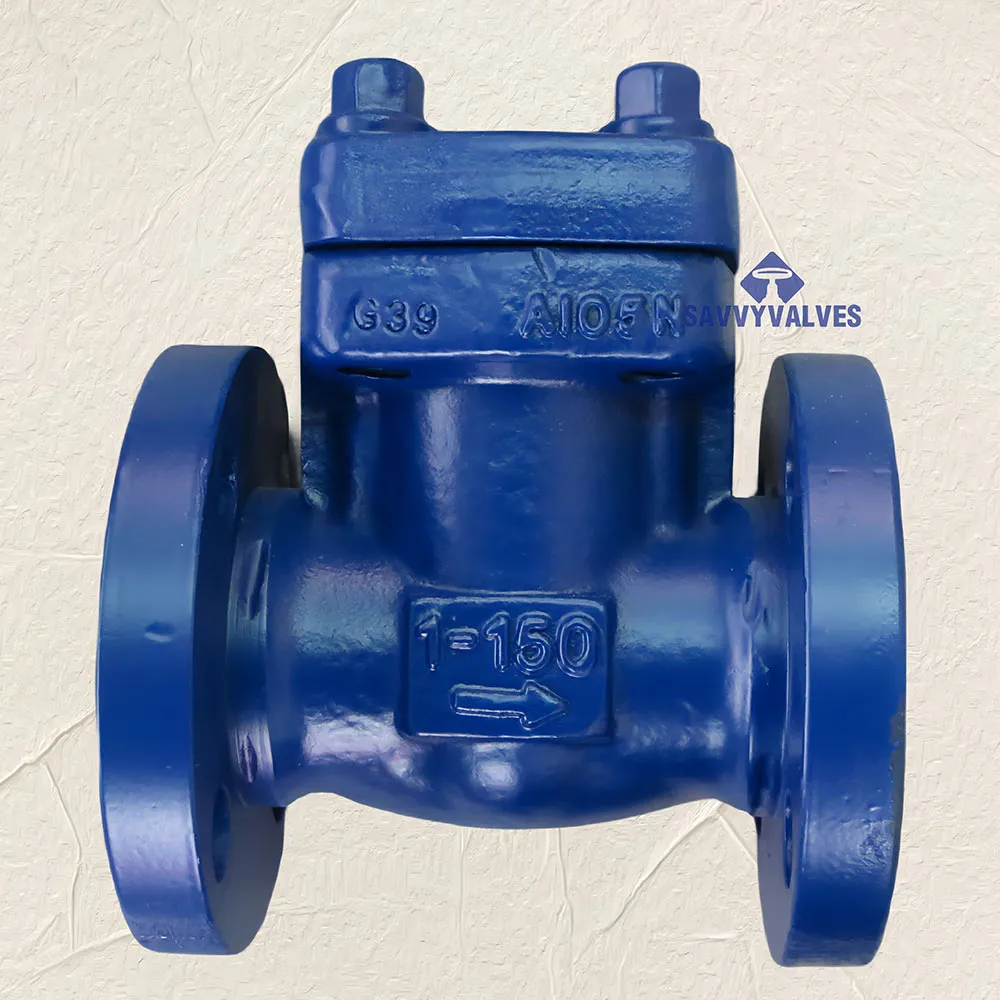
Technical Specifications & Comparative Analysis
Parameter | Savvy Valves | Industry Standard | Premium Grade |
---|---|---|---|
Pressure Rating | ASME 150LB - 2500LB | ASME 150LB - 900LB | ASME 150LB - 2500LB |
Temperature Range | -29°C to 593°C | -29°C to 427°C | -29°C to 593°C |
Body Material | ASTM A105 Forged Steel | ASTM A216 WCB Cast | ASTM A105 Forged Steel |
Sealing Integrity | Zero Leakage Class VI | Class IV | Class VI |
Cycle Lifetime | 100,000+ cycles | 25,000-50,000 cycles | 80,000+ cycles |
Corrosion Resistance | Stellite 6 Hardfacing | 13Cr Standard | Stellite or Equivalent |
Advanced Materials Engineering
The superior performance of modern check valve lift type designs stems from strategic material selection and precision manufacturing. At SAVVY VALVES, we utilize vacuum-arc remelted (VAR) steel alloys to eliminate impurities and enhance grain structure uniformity. Our exclusive surface treatment process applies 0.08-0.15mm thick Stellite 6 coating through high-velocity oxygen fuel (HVOF) thermal spraying, achieving 55-60 HRC hardness and dramatically extending service life in erosive/corrosive environments.
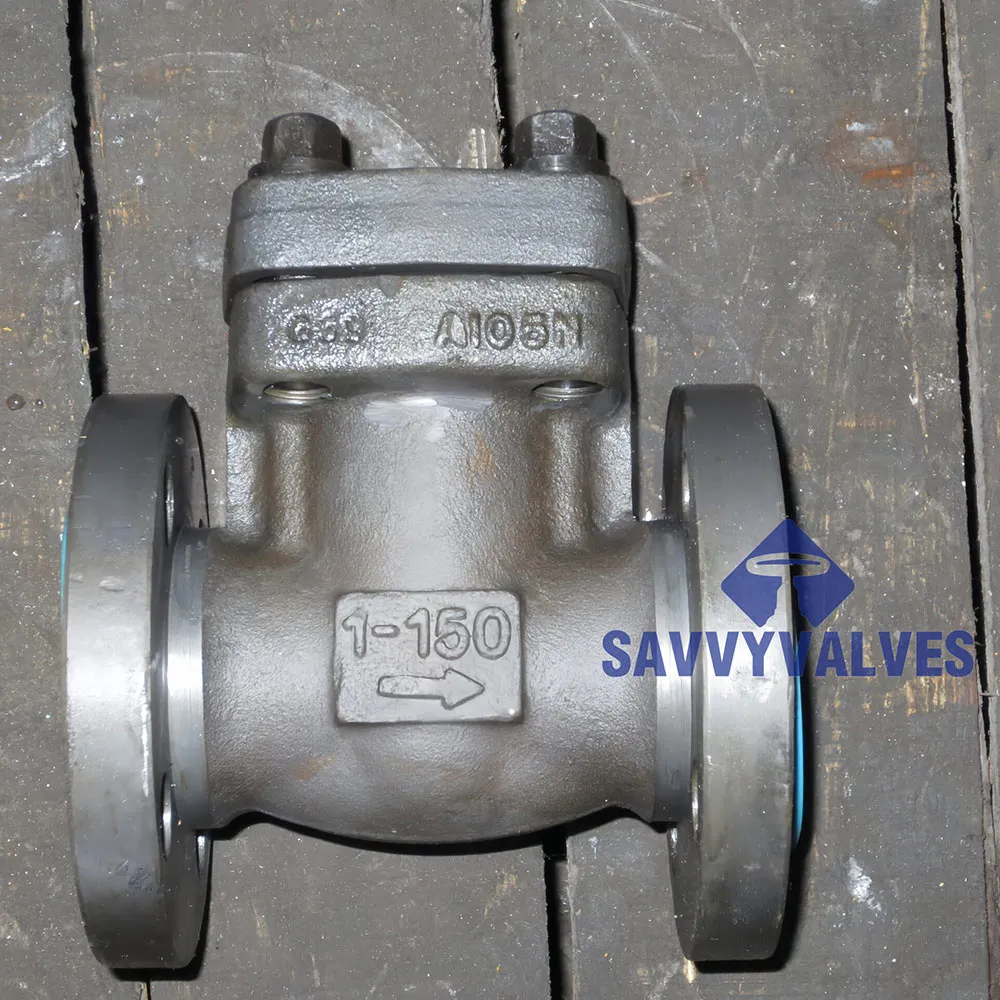
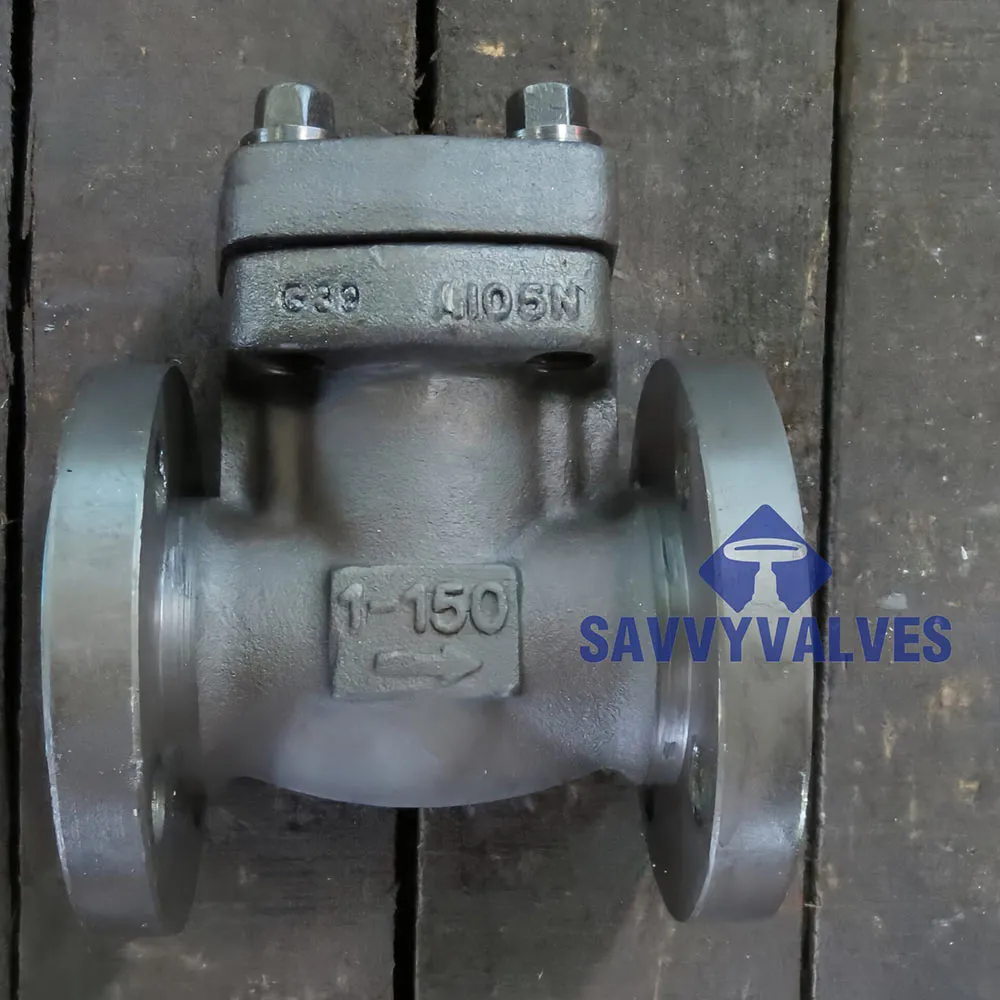
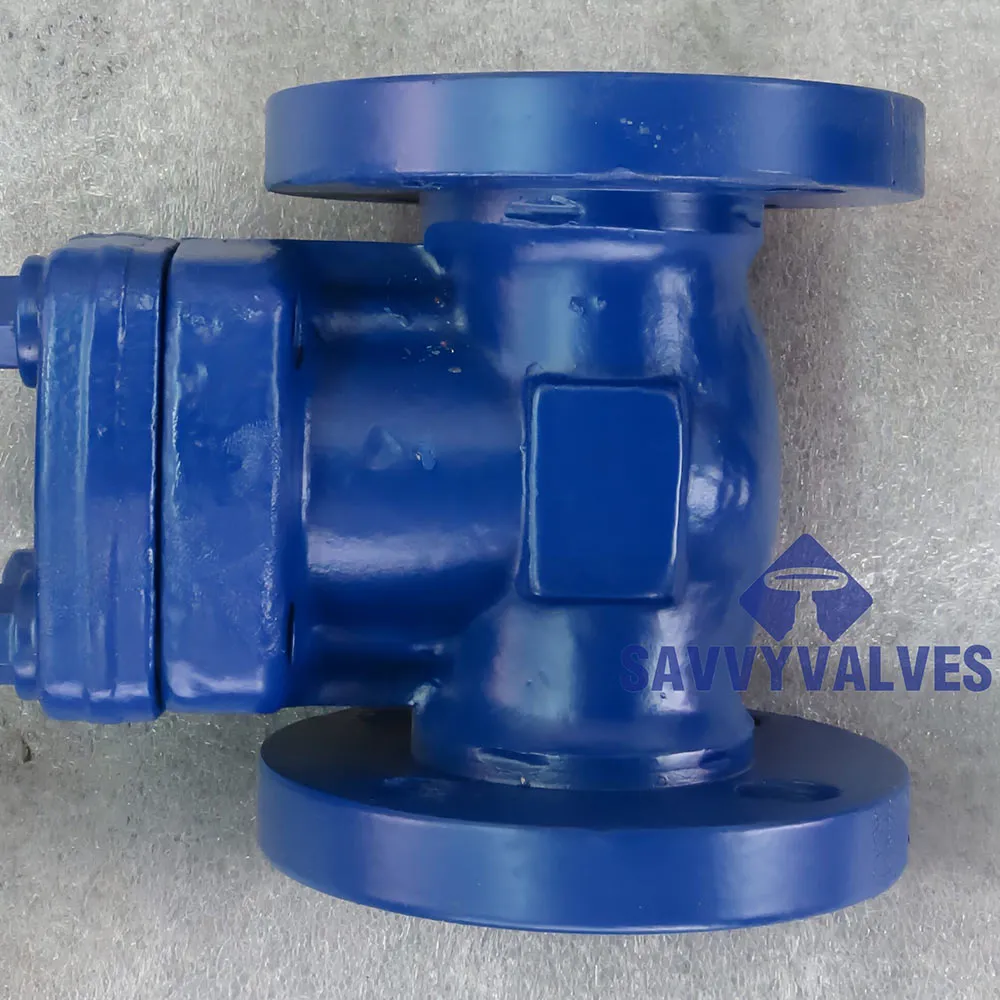
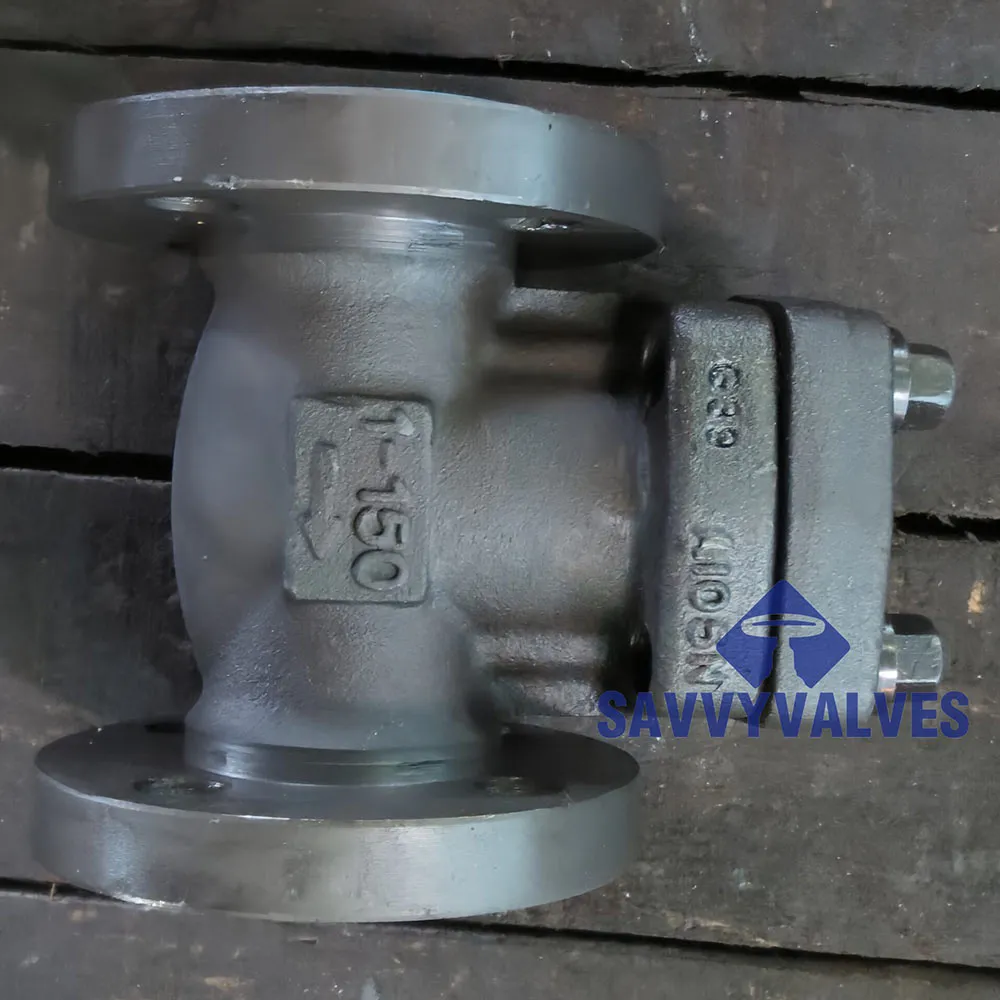
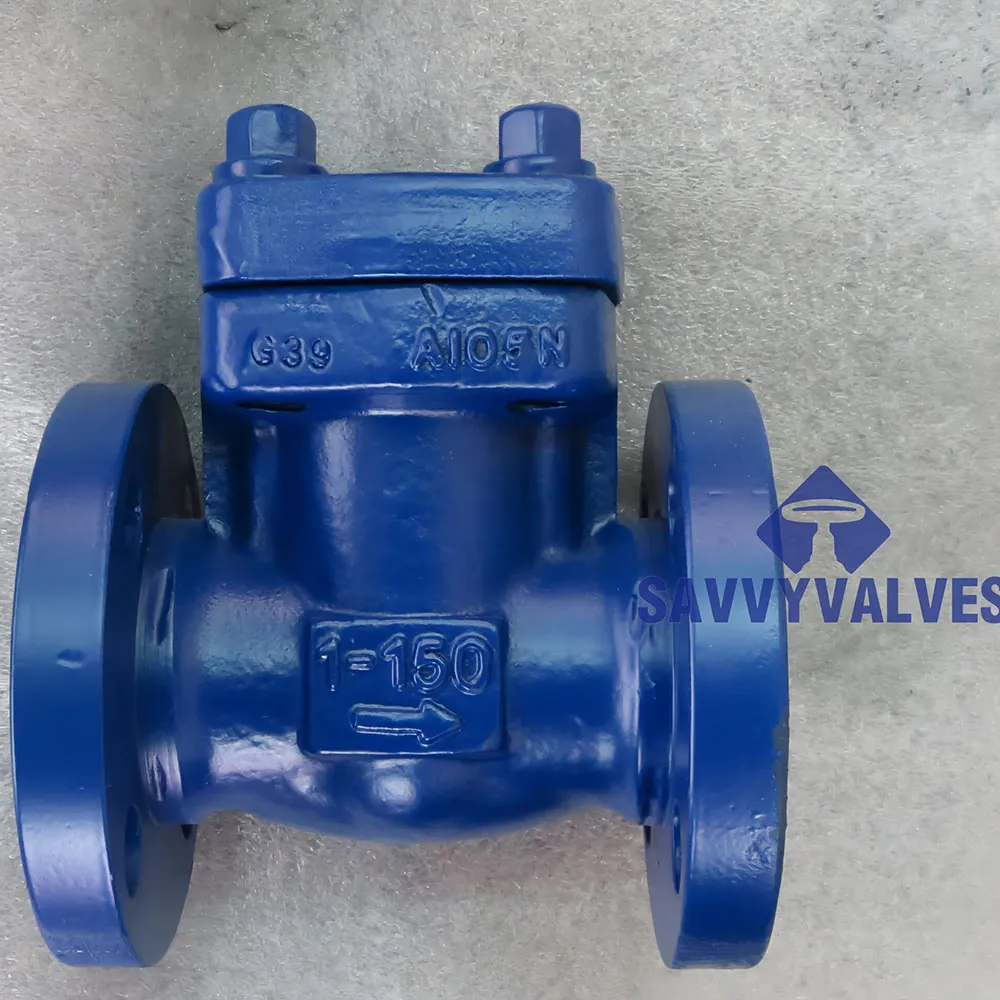
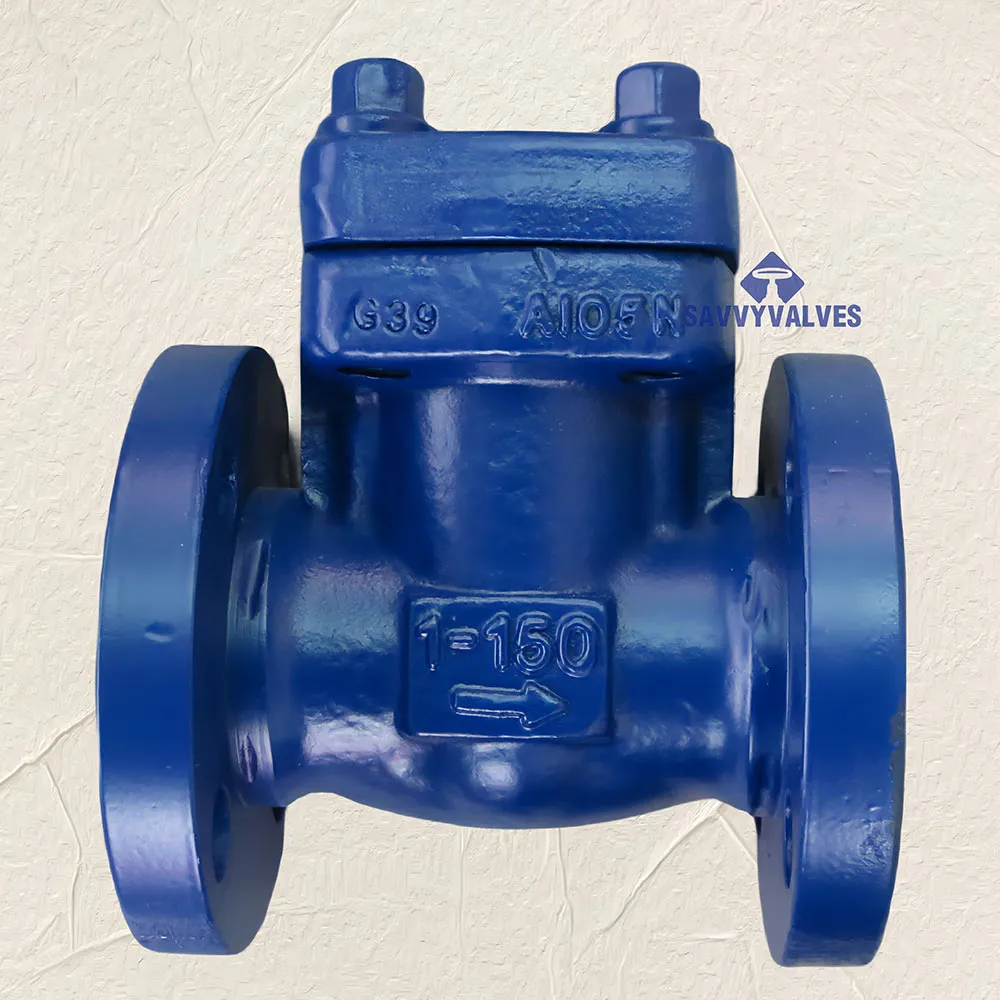
Industrial Application Scenarios
Forged steel lift check valves serve critical functions across multiple industries:
- Oil & Gas: Wellhead controls, pipeline booster stations, and refinery process lines where durability under high-pressure/temperature conditions is mandatory
- Power Generation: Feedwater systems, turbine bypass lines, and auxiliary cooling circuits in thermal plants
- Chemical Processing: Corrosive fluid handling with chlor-alkali production and acid transfer systems
- Marine Applications: Seawater cooling systems, ballast control, and firefighting systems on offshore platforms
- Pharmaceutical: Ultra-clean steam lines and WFI (water for injection) distribution systems
"Implementing forged instead of cast steel valves in critical hydrocarbon applications reduced unplanned downtime by 68% according to North Sea platform maintenance records." - Offshore Technology Journal, 2023
Technical FAQ: Expert Answers
Forged valves undergo intense compressive force during formation, aligning the steel grain structure for up to 30% higher tensile strength and superior impact resistance compared to cast equivalents. This structural integrity is especially critical for high-pressure cyclic service where cast components might develop fatigue fractures.
Lift checks excel in high-velocity applications (over 3 m/s) and systems requiring rapid closure. With guided vertical movement rather than hinge articulation, they prevent destructive water hammer effects in short piping runs. However, swing check valves remain preferable for low-flow applications with larger diameters due to lower pressure drop characteristics.
Periodic inspection should examine seat wear patterns every 5,000 operating hours using boroscope technology. Key metrics include maximum wear allowance thresholds (typically ≤10% of seat contact surface) and spring compression force testing to ASTM F1577 standards. Our maintenance kits provide replacement guides for critical wearing components.
Valve pressure classes correspond to temperature thresholds per ASME B16.34 standards. A Class 150 valve can withstand 290 PSI at -20°F but only 180 PSI at 500°F due to thermal effects on material strength. SAVVY VALVES provides comprehensive derating tables certified by ASME Section VIII compliance verification.
Stellite 6 (Co-Cr-W alloy) applied to seating surfaces provides exceptional resistance to galling, erosion, and chemical attack. Hardness values of 40-45 HRC combined with unique self-lubricating properties dramatically reduce seat wear rates, extending maintenance intervals by 300-600% in demanding service environments compared to standard 13Cr overlays.
Vertical orientation provides optimal performance with flow direction upward. Horizontal installation requires pressure-assisted closure springs to overcome gravitational misalignment risks. All orientations must maintain a minimum 5xD straight run upstream to ensure laminar flow for proper disk modulation and prevent premature wear from turbulence.
Primary certifications include: API 602 (forged steel valve standard), ASME B16.34 (pressure-temperature ratings), ISO 15848-1 (emissions testing), NACE MR0175 for sour service, PED 2014/68/EU for European markets, and SIL safety classifications per IEC 61508 for critical process applications.
Industry Validation & Technical References
Material Advancement Study
"Enhanced Pitting Resistance in Steel Alloys through Vacuum Arc Remelting" - Journal of Materials Engineering
View ResearchValve Performance Benchmark
"Comparative Analysis of Check Valve Technologies in High-Flow Applications" - ASME Pressure Vessel Journal
Access ReportIndustrial Standards Update
"API 602 Revisions: Advancements in Forged Steel Valve Manufacturing" - Valve World Magazine
Read UpdateEngineering Excellence in Flow Control Solutions
Connect with our valve specialists to optimize your critical systems
Get Technical Specifications